Author |
Message |
   
Searcher
Senior Member Username: searcher
Post Number: 592 Registered: 10-2004
| Posted on Sunday, December 22, 2013 - 10:18 pm: |
|
I have a soft spot for old carburetors and I couldn't pass this one up. It is rare to find a carburetor where the intended use is stamped right on the tag. I was especially tickled when I found the patent documents for it. The bronze bowl for this carburetor was not annealed after being spun. The result is rather typical in that multiple stress cracks have formed in predictable patterns. A previous owner soldered the cracks but he didn't make sure the cracks were all tightly snugged up first. Consequently, the bowl is now a hair wider at the top than it should be. New cracks have formed since the previous repairs were made. I've pondered placing the bowl into the muffle furnace at a temperature that would both melt the solder out and anneal the bowl. Then how would I repair the bowl so it could be used? I have no doubts somebody on the OME site has dealt with this problem before. Any and all suggestions would be most welcome.
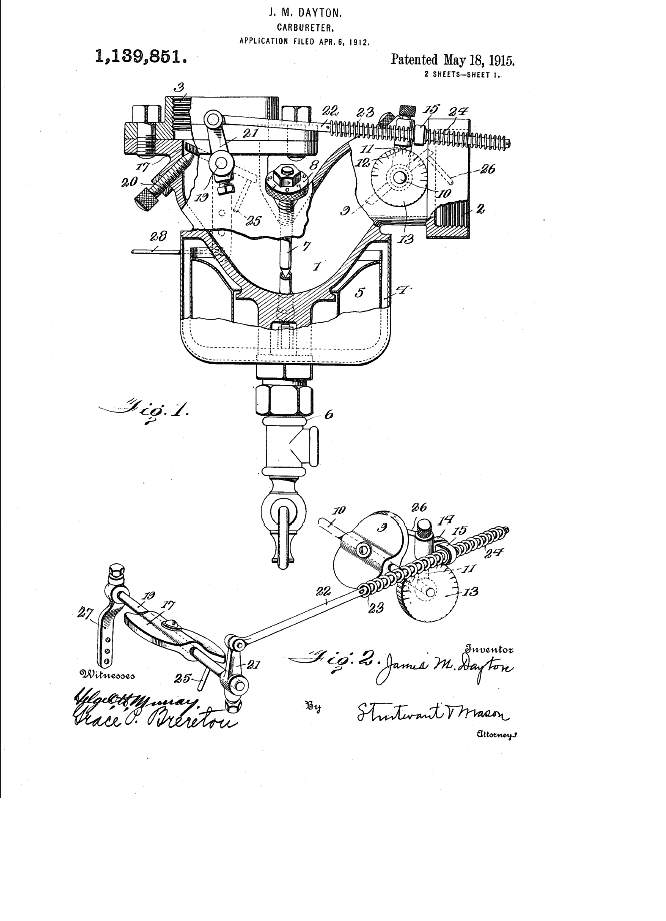 |
   
miro forest
Senior Member Username: miro
Post Number: 734 Registered: 11-2001
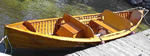
| Posted on Saturday, January 25, 2014 - 04:54 pm: |
|
That's a pretty heft wall thickness of the bowl ro have been spun. If it was mine to do, I'd get it close dull red as you can, having a stainless steel screw clamp ready, or maybe even figure out a way to get the clamp on before it went into the furnace, tighten the screw clamp and chill in water. But before doing that, I'd like to get the measurements and pictures in detail. As a Plan B, I'd think about spinning a replacement bowl before I tackled the repair of the original. As a Plan C, maybe a cast bowl might be the answer using the un-repaired, but smoothed original as a pattern. Ironically, the shrinkage on a cast brass replacement might just be enough to have the thing fit the carb. Miro |
   
Searcher
Senior Member Username: searcher
Post Number: 602 Registered: 10-2004
| Posted on Tuesday, January 28, 2014 - 05:22 pm: |
|
Miro, thanks for responding. The bowl ranges in thickness from 0.041" to 0.052" so it is a bit heavier than most spun brass I have seen. I've been thinking about your Plan A and doing some research. The melting point of red, yellow and admiralty brasses falls between 1650-1720F (900-940C). Soft solders usually melt at 400F (190C) or lower. As a practical matter, heating brass to 700F (357C) is sufficient to anneal it. The range between annealing and melting is wide enough so there is considerable cushion in the event the furnace thermocouple is off a little. At 700F a lot of the solder on the bowl should run off the surface leaving just a thin skin of solder behind. Same with any solder that is within the cracks, the excess will run off but some will remain within the cracks. If the rim of the carburetor could be clamped very rapidly as you suggest, the remaining solder within the cracks would not have time to solidify. On cooling, the solder remaining in the cracks might effect an almost instant repair. The tricks are going to be preventing solder from sticking the clamp solidly to the bowl and taking up the slack in the clamp before the solder has time to cool down to 400F. It�s worth a try. |
   
RichardDurgee
Senior Member Username: richarddurgee
Post Number: 3203 Registered: 11-2001
| Posted on Tuesday, January 28, 2014 - 06:57 pm: |
|
* 1912
* |
   
Searcher
Senior Member Username: searcher
Post Number: 604 Registered: 10-2004
| Posted on Tuesday, January 28, 2014 - 10:13 pm: |
|
The cross section and parts identification in that illustration are most helpful. Thanks. |
   
Andrew Munns
Senior Member Username: johnoxley
Post Number: 112 Registered: 04-2010
| Posted on Wednesday, January 29, 2014 - 12:32 am: |
|
Best option if the carby is going back into a working boat is to replicate. Needs pattern + casting + machine shop. Second option is to remachine from a billet. If it were my carby, I'd Dremel or file out the solder, pull the bowl back into shape and bronze weld or silver solder up the cracks. This will also anneal the bronze and remove any residual stresses. A left field approach might be to drill the ends of the existing cracks and machine a ring in steel, bronze or stainless that is a shrink fit. Use this to pull in the bronze bowl and then re-solder after a citric acid pickle. |
   
Searcher
Senior Member Username: searcher
Post Number: 605 Registered: 10-2004
| Posted on Wednesday, January 29, 2014 - 10:19 am: |
|
Thank you for responding. I like low tech options like Miro's Plan A and the third option that you mention here. I can try those without getting into a lot of expense. Is there any material that one could use to pack around the bowl that would tend to draw the solder away as the bowl is heated in a furnace or with a torch? In my first post, I referred to the bowl as bronze which of course it is. Then I start looking at melting point of brass? I will use age as my excuse for the lapse. |
|
|
|
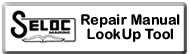

|