Author |
Message |
   
martinwill
Member Username: martinwill
Post Number: 14 Registered: 03-2007
| Posted on Monday, June 18, 2007 - 05:04 am: |
|
I am looking into the keel cooling idea instead of raw water for my engine. its a petter 16.4hp motor in a fiberglass hull, does anyone have any surjestions on cooler construction such as what length, diameter and pipe material (copper?) would be suitable, are there any formulas for working these things out ? |
   
miro
Senior Member Username: miro
Post Number: 281 Registered: 11-2001
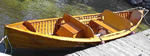
| Posted on Monday, June 18, 2007 - 12:04 pm: |
|
You should be able to calculate the heat transfer required e.g. assumptions might be: engine water exit temperature engine water flow rate temperature of external water at the keel efficiency of the material that you are using for piping for heat transfer desired water temperature coming back into the engine These will let you calculate the surface area needed for the heat transfer. Then you would simply convert this to the piping length you need to achieve that surface area. Keel coolers were used in the 1960's on small steam launches as condensers to create a vaccuum and thus increase the efficiency of the steam plant in the boat. Weston Farmer's book - From My Old Boat Shop might have some further details on condensers that you might be able to use for keel cooling. I also recall that there are heat exchangers for medium and larger motor yachts that might give you some help. miro |
   
martinwill
Member Username: martinwill
Post Number: 15 Registered: 03-2007
| Posted on Tuesday, June 19, 2007 - 04:24 am: |
|
thanks for that, will have to fit a dry exhaust as well or run a seperate pump to cool the wet exhaust. still in two minds wether to run a keel cooler or leave it raw water cooled. |
   
richardday
Senior Member Username: richardday
Post Number: 505 Registered: 11-2003
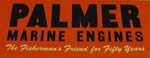
| Posted on Tuesday, June 19, 2007 - 06:36 pm: |
|
Around the Chesapeake Bay the typical keel cooler was simple. One ran a length of 3/4" or 1" copper pipe from near the stern of the boat to near the bow along side the keel rubbing strip made a U turn at the bow and returned to the stern area. All very scientific I should add. At the stern two through hulls connected to the engine cooling system. The engine water pump circulated the coolant which was typically 50% fresh water and 50% automotive anti freeze. A small vertical expansion tank was installed along side the engine. This typically was a 20 to 30 inch length of copper pipe about 3 inchs in diameter. The bottom cap of the exspansion tank was brazed to the pipe and the top cap had a small hole drilled in it for pressure relief. Pull the cap off to check the level of the coolant and nothing was complicated. If the engine was a V-8 two very hot dry exhaust mufflers stood up at the aft eng of the engine and when in dock typically a National Bo or now also long gone Gunther were the preferred wet weather caps. Hey nobody thought it was rocket science. And it gets cold out there on the bay on ocasion so one needs a little pick me up!!! The preferred engine was the Olds 455 with Barr conversion hardware. Hard to beat. Most are now long gone and only fond memories. Hard to believe you could buy a New 455 Olds engine in 1970 for $550.00. It had no exhaust manifold but it did have a marine fuel pump and carburetor. The exhaust manifolds from Barr were $75.00 each. Reverse gear $650.00. Sea water pump and oil cooler about another $100.00. I had 900 hours on mine when it ate a valve. A marvelous engine and one that will long be remembered by the watermen of the Chesapeake Bay. |