Author |
Message |
   
jb_castagnos
Senior Member Username: jb_castagnos
Post Number: 1227 Registered: 07-2002
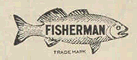
| Posted on Sunday, October 30, 2016 - 10:23 pm: |
|
Bob sent his crank to me for repairs. The mains had been welded once before, both ends were bad, no centers. I decided to make a new one, cut it out of 1 1/4" plate, put centers on it and started making it round. I worked between the lathe and grinder, have it roughed out. To be continued.
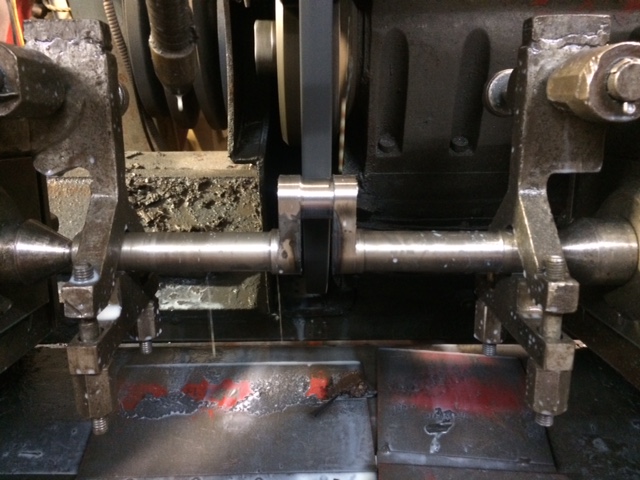 |
   
richarddurgee
Senior Member Username: richarddurgee
Post Number: 3903 Registered: 11-2001
| Posted on Sunday, October 30, 2016 - 11:13 pm: |
|
* JB It looks great ! To bad hand a made crank this pretty has to get covered with a crankcase ! * |
   
david_doyle
Senior Member Username: david_doyle
Post Number: 97 Registered: 03-2013
| Posted on Monday, October 31, 2016 - 01:40 am: |
|
JB, Really appreciate seeing your work. Much thanks for sharing. |
   
kayak
Advanced Member Username: kayak
Post Number: 40 Registered: 06-2016
| Posted on Monday, October 31, 2016 - 01:57 am: |
|
amazing! what type of steel is that? was the notch cut out with a band saw? were the ends of the thick center piece drilled to accept the end shafts? |
   
johnoxley
Senior Member Username: johnoxley
Post Number: 164 Registered: 04-2010
| Posted on Monday, October 31, 2016 - 02:36 am: |
|
Built one like this for a 3" stroke two cylinder steam engine. Roughed out from 1.25" slab and heat twisted centre of shaft in big lathe to get 90 degree crank offset, then finish machined at low speed with broad faced tool (Water finish). Hate to have to pay for this sort of work. |
   
jb_castagnos
Senior Member Username: jb_castagnos
Post Number: 1228 Registered: 07-2002
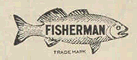
| Posted on Monday, October 31, 2016 - 06:39 am: |
|
It was cut with a torch from a piece of 1 1/4" steel, part of an in ground auto lift I saved for the steel. I usually get the steel from my son, they manufacture dredges, he gets the better grade of steel, don't remember the #. This is a small crank, I put the coarse narrow wheel on the grinder and ground the throw out, swung the crank back and forth by hand until it was close then let it rotate. My son brought a piece of 2" steel, making a new crank for the Buffalo, going to cheat on this one, a friend is going to water jet it for me, will save a lot of work. John, here's a link to the 3 cylinder crank I twisted. http://www.oldmarineengine.com/discus/messages/2/259117.html |
   
david_doyle
Senior Member Username: david_doyle
Post Number: 98 Registered: 03-2013
| Posted on Monday, October 31, 2016 - 01:27 pm: |
|
"you're twisting them while they're square, you're setting up a stress. Turn them round, twist them, finish turning" Exaclty how much is a piece of knowledge like that worth! Priceless. I feel like a bandit everytime you guys share these gems. } |
   
jb_castagnos
Senior Member Username: jb_castagnos
Post Number: 1229 Registered: 07-2002
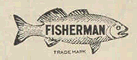
| Posted on Monday, October 31, 2016 - 01:43 pm: |
|
Went in this morning before work, milled the cheeks of the throws to proper width and finished in the grinder, still oversize. A picture of the plate I cut it from, don't know what it is, machines well, better than cold rolled.
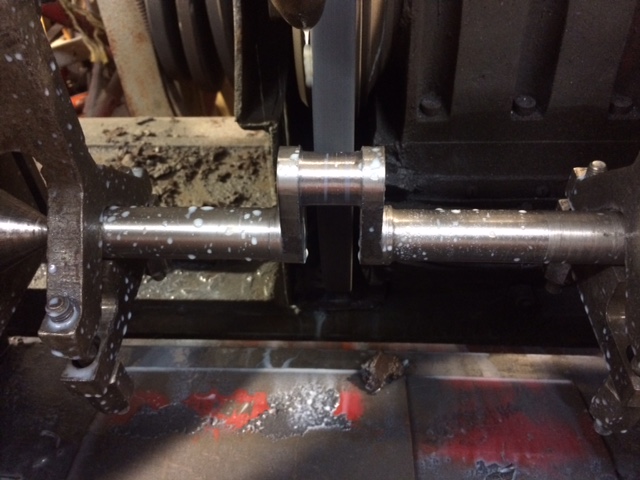 |
   
jb_castagnos
Senior Member Username: jb_castagnos
Post Number: 1231 Registered: 07-2002
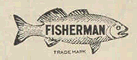
| Posted on Monday, October 31, 2016 - 09:53 pm: |
|
I went in tonight and I put a fine wheel on the grinder, dressed it and roughed in the mains .030. The Arnold gauge will read from here, allows you to measure while you're grinding. The gauge reads a minimum of 1", OK for the mains, won't read the rod or the ends of the crank. While roughing it in I used the dial stop and it's fairly close, will have to watch it.
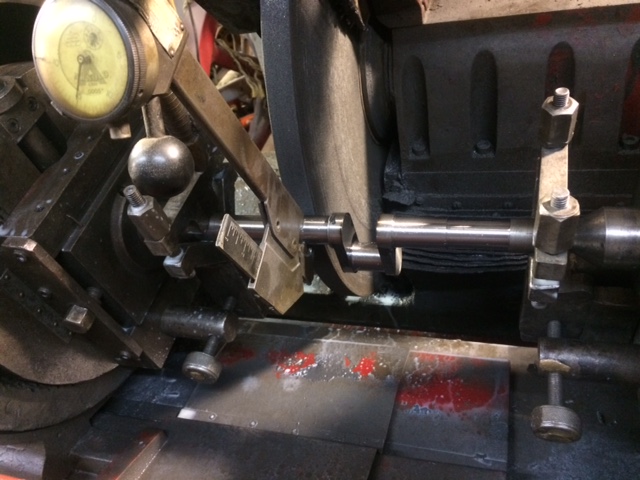 |
   
billschaller
Senior Member Username: billschaller
Post Number: 655 Registered: 12-2003
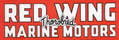
| Posted on Tuesday, November 01, 2016 - 04:37 am: |
|
Great work. I bet your new one is a bit stronger than the original. It would be interesting to know whether the original company made their own, or source it out.
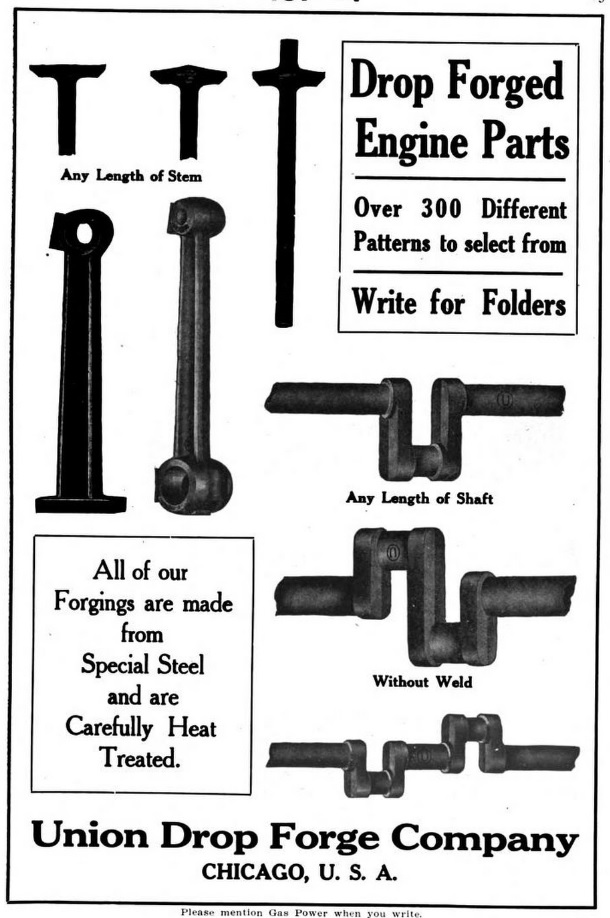 |
   
kayak
Advanced Member Username: kayak
Post Number: 42 Registered: 06-2016
| Posted on Tuesday, November 01, 2016 - 03:15 pm: |
|
Found this quick little video showing a production forged crankshaft being made including the visit to the twisting machine. EDIT:youtube seems to have switched the video or there is an error. I still have the original up in a window and will try to save it now. It's pretty good, concise and shows the steps. OK, re-saved it to my own channel. https://youtu.be/Sth7tULPwHQ |
   
kayak
Advanced Member Username: kayak
Post Number: 43 Registered: 06-2016
| Posted on Tuesday, November 01, 2016 - 03:46 pm: |
|
This is the correct forging crankshaft video: https://youtu.be/Sth7tULPwHQ |
   
jb_castagnos
Senior Member Username: jb_castagnos
Post Number: 1232 Registered: 07-2002
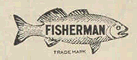
| Posted on Tuesday, November 01, 2016 - 10:04 pm: |
|
Bill, my guess is the subbed it out, there were companies like the one in your ad that specialized in this expensive equipment if you didn't keep it busy. The original crank was forged, St. Lawrence cranks were some of the ones I've seen cut from plate. I went in tonight and finished the crank. Bob will take it from here, cut to length and re center, bevel the throws at the rod journal end, key it, and radius the sharp edges on the throw. The first picture shows grinding the end with the live center I adapted to the machine, second is the finished crank.
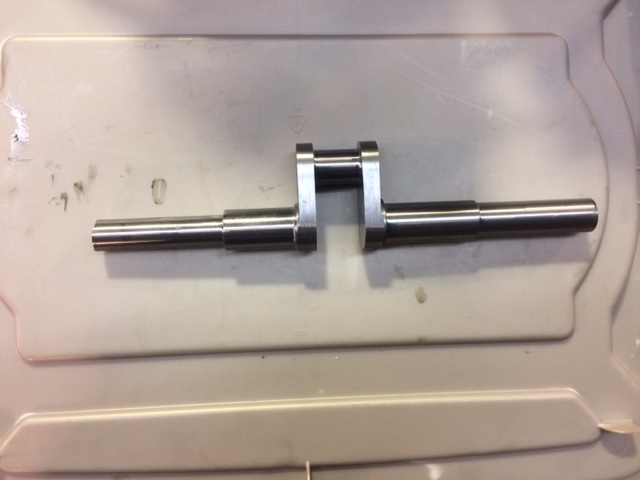 |
   
jb_castagnos
Senior Member Username: jb_castagnos
Post Number: 1233 Registered: 07-2002
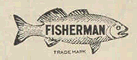
| Posted on Tuesday, November 01, 2016 - 10:07 pm: |
|
Kayak, thanks fir the video. I didn't realize until I did the 3 cylinder crank that automotive cranks were twisted, top of the line race car cranks are forged 90 degrees, a lot more $. |
   
jb_castagnos
Senior Member Username: jb_castagnos
Post Number: 1234 Registered: 07-2002
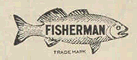
| Posted on Tuesday, November 01, 2016 - 10:14 pm: |
|
Richard, I agree, hate to put it in a crankcase, at least you've gotten me taking pictures. |
   
richarddurgee
Senior Member Username: richarddurgee
Post Number: 3905 Registered: 11-2001
| Posted on Wednesday, November 02, 2016 - 08:28 am: |
|
* JB Most of us on this site appreciate your work and the photos bring it to us and keeps us in the loop! For years I have said that these old engines are an art form, the hand made pieces are in a category of their own. I saw this definition and thought it most applicable here.
Most sculpture as we know it sits on a pedestal or hangs on the wall, we are fortunate to add the dimension of sound when its put together and running. In the above Definition its usage in verb form Says " the choir stalls were each carefully sculptured " I think that crankshaft you made was carefully SCULPTURED ! Good Stuff !! * |
   
david_doyle
Senior Member Username: david_doyle
Post Number: 99 Registered: 03-2013
| Posted on Wednesday, November 02, 2016 - 11:29 am: |
|
wow, tres bon! |
   
jb_castagnos
Senior Member Username: jb_castagnos
Post Number: 1236 Registered: 07-2002
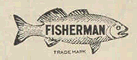
| Posted on Wednesday, November 02, 2016 - 03:50 pm: |
|
Merci beaucoup, "Da veed". |