Author |
Message |
   
herbertchoover
Member Username: herbertchoover
Post Number: 26 Registered: 04-2016

| Posted on Friday, May 20, 2016 - 02:14 am: |
|
ok, this issue is going to come up eventually so, looking for suggestions - especially ones that might be appropriate for the era of this engine , 1920's to 1940's - although that may not be possible. to preserve the YT1, there will be a keel loop with automotive coolant (zero pressure with vented expansion tank), no raw water. unfortunately, that leaves the issue of cooling the exhaust. Ernie suggested one possibility of running a small pulley at the flywheel nut and belt driving a Jabsco bronze 1/4" raw water pump. One issue with that is interference with the starting peg. It also takes away some of the appeal of the engine by cluttering it. another idea is to run a small rubber tire on the jabsco pump pulley and run that against the flywheel. another idea I had which is the most elegant looking, would be to sister another small reciprocating pump along side the existing cooling pump. of course one must be careful on linkages and offset-loads etc. again, need to preserve the engine. another user made a suggestion to run dry exhaust pointed straight up. but would need to shield that muffler and of course the exhaust would be in the air and that would be quite noisy. I like water cooling best. a "modern" approach would be to use an electric pump, but there is no generator so the battery would be drained with that. plus its too "modern". looking for ideas as folks here have seen all the old gizmo's that I havent. |
   
richardday
Senior Member Username: richardday
Post Number: 1132 Registered: 11-2003
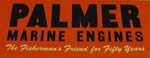
| Posted on Friday, May 20, 2016 - 09:54 am: |
|
How about a small scoop ahead of the propeller so it pushes water with a return bend into the exhaust well below the level of the head exhaust. It seems to me you will not be idling the engine for long periods and and therefore would be the recirculating head coolant keeping the head and vertical exhaust area cool enough but from the outside of the vertical section. The idle prop would simply let sea water flow into the aft exhaust line to keep it cool enough for any fire hazard would have the prop wash water introduced at the junction with the vertical section of the exhaust line. A little experimenting could prove the possibility of such an approach. I would want a test cock at the inboard end of the horizontal section of the exhaust line to make sure before starting the line is full of sea water. |
   
ernie
Senior Member Username: ernie
Post Number: 2283 Registered: 01-2002
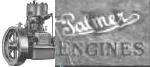
| Posted on Friday, May 20, 2016 - 11:00 am: |
|
No I did not say a small pulley under the flywheel nut. I was referring to a Palmer BH installation which already has a pulley under the flywheel nut and no crank handle. I did suggest a small Jabsco type pump mounted low near the bottom of the flywheel with a rubber drive wheel running on the flywheel OD. The pump shaft would be parallel to the crankshaft. Been done many times over the years, works well and no belt to worry about. |
   
herbertchoover
Member Username: herbertchoover
Post Number: 27 Registered: 04-2016

| Posted on Friday, May 20, 2016 - 01:09 pm: |
|
hi ernie, thanks. to clarify, I recall u describing to me a pulley with a blank center that can be drilled and tapped to flywheel nut threads and replaces the flywheel nut. but Im new at this so maybe misheard u? I like the small rubber tire option as u described, so I will post a Wanted ad for a pump. if anyone has a small jabsco I would be most interested! regards, chris |
   
herbertchoover
Member Username: herbertchoover
Post Number: 28 Registered: 04-2016

| Posted on Saturday, May 21, 2016 - 02:20 pm: |
|
Update, someone sold me a 2620 Jabsco pump - I just need to determine a source (McMaster, Grainger, other?) for a drive roller as Ernie helpfully suggested. I am open to suggestions, especially on sizing. Looking at the pump specs, Ithink 3" to 4" which at 500 motor rpm would be 1500 to 2000 pump rpm, about right. Making a spring-loaded bracketry is another matter. As always, any pictures would help. Since Ernie said this has "been done many times" hopefully someone sees this and can post a picture. Also, ordered a 1/8" holes bronze raw water pickup grate, a 1" bronze through hull for exhaust, and found 9ft of 1" ID exhaust hose. Ernie had also made a suggestion to add water to the exhaust at the first elbow which points down by drilling and tapping the elbow for a compression fitting, and straight boring the fitting to a copper tube can pass all the way through the fitting into the downstream of the exhaust. A small rubber hose from that to the pump should finish off that plumbing (I can double flare the tube to make it a barb). as always thoughts and suggestions appreciated, and I hope these posts will help others in the future. |
   
ernie
Senior Member Username: ernie
Post Number: 2285 Registered: 01-2002
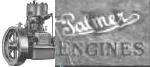
| Posted on Saturday, May 21, 2016 - 04:59 pm: |
|
use a hockey puck |
   
billschaller
Senior Member Username: billschaller
Post Number: 647 Registered: 12-2003
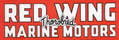
| Posted on Monday, May 23, 2016 - 12:30 pm: |
|
Here is one way it was done back in the day. Prop shaft bilge pump. 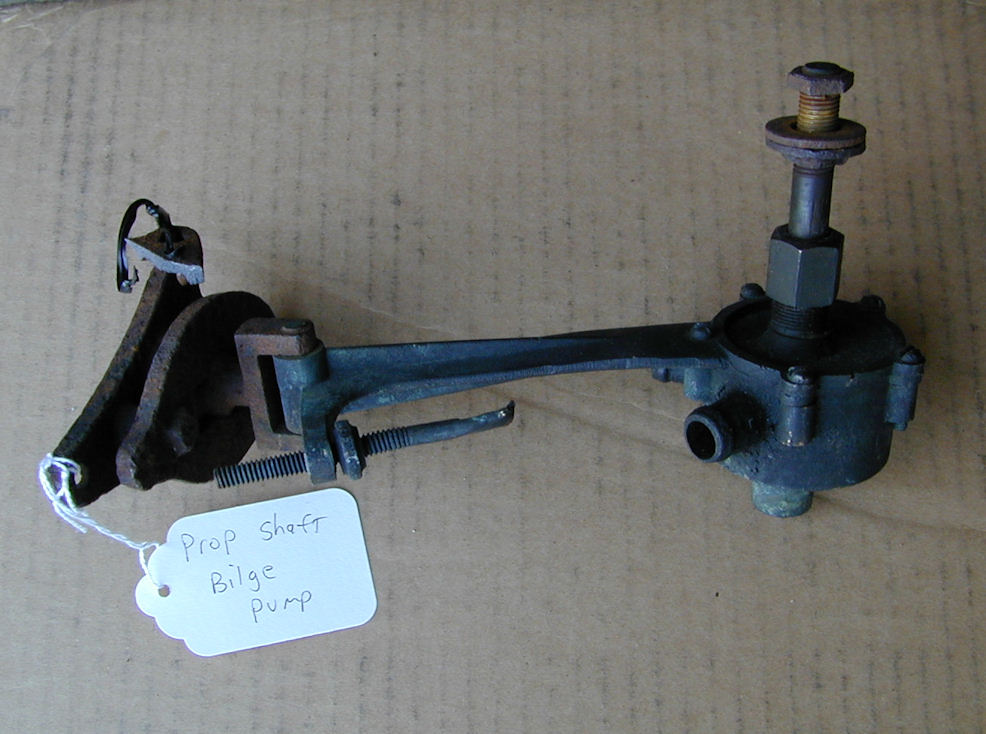 |
   
miro
Senior Member Username: miro
Post Number: 871 Registered: 11-2001
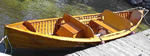
| Posted on Monday, May 23, 2016 - 10:10 pm: |
|
I think virtually any water that you can introduce into the exhaust stream as soon after the exhaust port will help a lot. Doesn't have to be a huge volume , in fact a dribble will likely do it. Anything to cool the gases will be of great benefit. Look at some of the videos of JB's camp and I think one of them shows the water dribbling over the side - the boat has dry, loud exhaust. I suppose that you could calculate the volume (gal per minute) by measuring the cooling pump (dia and stroke) , then using say 600 RPM, estimate the volume of water made by that pump. With some luck, you can then estimate the speed of your raw water pump to give that volume ( or less) Miro |
   
louq
Member Username: louq
Post Number: 13 Registered: 09-2010
| Posted on Wednesday, May 25, 2016 - 09:19 pm: |
|
I had a small pulley machined fron bronze stock to fit between the gearbox and the engine flanges. This way the pump is always running when the engine is. It has a 3/8" belt groove to drive an antique Jabsco pump with rubber impeller and grease cups for lubrication. It pumps plenty of water to keep things cooler. Lou |
   
herbertclarkhoover
New member Username: herbertclarkhoover
Post Number: 1 Registered: 05-2016
| Posted on Friday, May 27, 2016 - 06:21 pm: |
|
hi lou, thanks. in my case the gearbox mates the engine and no shaft is exposed. I have a jabsco pump and hockey puck per ernie's suggestion. now need to make the bracketry, a spring, and attach the 3" puck to a pulley so the puck can ride against the outside of the flywheel. it wont be in the way of cranking the engine. the pulley may allow me to run a kubota mini alternator too. |
   
herbertclarkhoover
New member Username: herbertclarkhoover
Post Number: 2 Registered: 05-2016
| Posted on Friday, May 27, 2016 - 06:24 pm: |
|
btw my account got screwed up when I tried to fix the display name and the lack of email alerts. andrew was going to fix it but hasnt yet so I started a new account. this board software doesnt allow capital letters or special characters apparently (but doesnt tell u that when setting up the profile). whatever, as long as it works! |