Author |
Message |
   
rshields
New member Username: rshields
Post Number: 1 Registered: 02-2013
| Posted on Monday, April 01, 2013 - 02:42 pm: |
|
I am in the process of rebuilding an Atlantic 4 hp. Has anyone had any experience with coating the inside of the water jacket with either a paint or the 'rust converter' product that changes rust to a polymer by reacting with the rust, to stop the continuous rusting of the casting. The engine I have was stored in Edmonton Alberta (dry climate( for 25 years and was working when it was first stored. However, the water jacket was completely filled with rust and cracked the casting, so I would like to stop any more of the rusting process if possible. OR any other suggestions would be appreciated. |
   
qwilkin
Senior Member Username: qwilkin
Post Number: 78 Registered: 08-2009
| Posted on Monday, April 01, 2013 - 05:13 pm: |
|
I have seen many photos of engines restored and the brass parts are so well polished . I have a blaxland twin engine which I am restoring and many of the brass parts are coverd in paint . I had a carb overhauled some time back and it came back gleaming as if it had been submerged in a solution . Can anyone help please as to what to use . Thank You Quinton |
   
richardday
Senior Member Username: richardday
Post Number: 1055 Registered: 11-2003
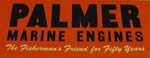
| Posted on Monday, April 01, 2013 - 08:39 pm: |
|
Your only hope in my opinion is high temp controlled heating to drive the salt out of the pores of the cast iron. No Dip, No Acid, No Caustic soda is going to work. The temp needs to be controlled so you don't warp the structure and once you have the salt out of the iron then it can be welded/brazed etc. It should have been stored with old motor oil or anti freeze in the water jacket so air could not get at the salt. Your best hope is George Coates IV ([email protected])in Elkton, Maryland. You can see examples of their incredible work on salt poisoned cast iron on this page. |
   
robert
Senior Member Username: robert
Post Number: 540 Registered: 07-2003
| Posted on Monday, April 01, 2013 - 09:35 pm: |
|
Quinton, You can just use paint stripper to remove the paint. Simplest, easiest and least labour & cost. Once the paint is off you can decide whether you want to polish the brass or not. The carb shop probably used a dilute solution of muriatic acid. Nasty stuff to work with if you buy it full strength; vinegar works almost as well, but slower. If your brass work is sand cast it will probably be quite rough. If you're not equipped to smooth and polish castings your best bet is to take the parts to a polishing shop. You can save yourself some money if you file and hand sand the castings yourself as much as possible first. Some polishers are careful not to spoil the profile and shape of pieces; some are ham-fisted clowns who don't care. The rougher your parts are, the heavier, faster cutting abrasives they will use to polish them, and the more likely they are to deform them. That's why the smoother they are when you drop them off, the better and cheaper the job should be. Rotary cotton buffs are inclined to round everything they touch. In the old days I understand they used wet leather belts with powdered abrasive as these would conform to the shape of the object being polished and cause much less rounding & deformation. A lost art now I suspect. |
   
senojn
Senior Member Username: senojn
Post Number: 105 Registered: 08-2006
| Posted on Tuesday, April 02, 2013 - 02:31 am: |
|
Quinton ,Sir. I have mentioned this to you before ! Please post (ask questions) under an appropriate subject heading . You have asked your question under the heading of internal water jacket coatings . You have missed your audience and they have missed you! You could look under the many references (Search) at top of page ,for example polishing /cleaning/brass/copper etc. Your question is also covered under the Blaxland pages to the enth degree . I carefully use hydrochloric acid (swimming pools ) or vinegar and buff . Neil |
   
keith
Senior Member Username: keith
Post Number: 387 Registered: 02-2002
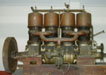
| Posted on Wednesday, April 03, 2013 - 09:13 pm: |
|
I would like to take this post back to the original question, and that is to a water jacket sealer. Anyone have any input? |
   
s.marsh
Visitor
| Posted on Wednesday, April 03, 2013 - 10:41 pm: |
|
Eastwood glyptal block sealer is what you need.The problem would be getting old interior surfaces clean enough for it to adhere. |
   
ernie
Senior Member Username: ernie
Post Number: 1630 Registered: 01-2002
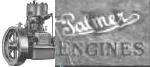
| Posted on Thursday, April 04, 2013 - 09:56 am: |
|
I use real zinc chromate paint thinned 50%. There is a Badly rusted and cracked salt water 3 HP Lathrop that I repaired the water jacket on over 15 years ago and it still has ho signs of rust in the jacket. I tried it on a piece of water jacket so I could see how it soaked in and the penetration through what ever was on the internal surface was real good |
   
axtion_jim
Advanced Member Username: axtion_jim
Post Number: 33 Registered: 11-2010
| Posted on Thursday, April 04, 2013 - 01:11 pm: |
|
My question is at what is considered a high enough controlled temparture to cook out the salt. From personal expearance I use a good wood fire in the yard and that must be over 500 degrees.It has beed suggested by others to use a electric stove, but I would like to know that all of the salt has been cooked out. |
   
robert
Senior Member Username: robert
Post Number: 544 Registered: 07-2003
| Posted on Friday, April 05, 2013 - 12:09 am: |
|
Self-cleaning ovens get up to around 850�, which should be good enough. Aside from being cheap and readily available, they also heat up and cool down slowly, which is important to avoid distortion I've always heard. A retired electric pottery kiln would be the next option, and a good one too, if you want to repair cylinders the way Mr. Coates does as you can heat the cylinder to whatever temperature you need for gas or arc welding without distortion or cracking. |
   
klanger
Member Username: klanger
Post Number: 21 Registered: 03-2012

| Posted on Friday, April 05, 2013 - 07:30 am: |
|
If using an old pottery kiln, for how long would you need to hold at temperature to ensure the salt has been expelled? And how would the cylinder be placed in kiln, packed in anything or just standing in the centre of kiln. I have access to an electric kiln and would like to treat and seal cylinder. Kev |
   
robert
Senior Member Username: robert
Post Number: 545 Registered: 07-2003
| Posted on Friday, April 05, 2013 - 10:35 am: |
|
This would be question to ask someone involved in museum conservation of marine artifacts or the conservation of steel structures in a marine environment. Is the salt actually expelled or is it 'converted' in some way? Or is the real advantage of this method to burn off all water, oils and other contaminants that have penetrated the metal over the years? That would allow any treatment to penetrate much further into the metal, and if applied while the metal is still warm and has not re-absorbed moisture from the air, the coating or treatment applied would prevent any moisture from again migrating into the metal, contacting the salts and restarting the process of oxidization. The key factor is the airtight nature of the coating and how long that sealing effect lasts. That's my understanding of the process for what it's worth. So AFAIK, the heat does not drive out the salts unless they are carried out by the expulsion of oils and water that in the metal as it is heated. |
   
scott_n
Senior Member Username: scott_n
Post Number: 227 Registered: 02-2008
| Posted on Friday, April 05, 2013 - 11:19 am: |
|
as fore question 2 I boil painted brass and bronze in TSP and water it removes the paint with no Mechanical cleaning |
   
ernie
Senior Member Username: ernie
Post Number: 1631 Registered: 01-2002
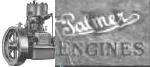
| Posted on Friday, April 05, 2013 - 12:40 pm: |
|
Sodium chloride, also known as salt, common salt, table salt, sea salt or halite, is an ionic compound with the formula NaCl, representing equal proportions of sodium and chloride. melting point 1474 deg F boiling point 2575 deg F So I guess going over 2575 deg F causes it to simply turn into a gas and leave where ever it was. Amazing what you can find on the net. Also amazing are all the other things we get to learn simply because we play with old engines. |
   
keith
Senior Member Username: keith
Post Number: 388 Registered: 02-2002
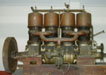
| Posted on Friday, April 05, 2013 - 09:58 pm: |
|
Ernie, So I'm not to bright. Do I heat the cast iron to 2575 degrees (for how long) and then treat with a 50% zinc chromate solution? I'm not being sarcastic but looking for a clear answer. I'm not sure the answer is out there. I'm not aware of museums treating marine artifacts using heat. ???????? |
   
axtion_jim
Advanced Member Username: axtion_jim
Post Number: 34 Registered: 11-2010
| Posted on Saturday, April 06, 2013 - 12:01 am: |
|
Ernie, That is the same formula I found when I went pooking around a web site connected to the pottery hobby. Maybe we can ask a potter how long it take to cook the salt out of the clay. I would think less time with cast iron parts. |
   
ernie
Senior Member Username: ernie
Post Number: 1632 Registered: 01-2002
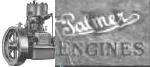
| Posted on Sunday, April 07, 2013 - 07:43 pm: |
|
I looked up NaCl SALT to find its melting and boiling points to answer a question on what happens to the salt in the iron when heated in a kiln. As to coating the inside of the jacket I have done 3 engines where the jacket was falling off. I cleaned the rust out of the inside and put the outer jacket back on with epoxy. Then coated the inside with thinned zinc chromate. These engines were not heated in a kiln. |
   
axtion_jim
Advanced Member Username: axtion_jim
Post Number: 35 Registered: 11-2010
| Posted on Monday, April 08, 2013 - 12:24 am: |
|
Ernie. Myself and my old friend Harvey used the fire trick, Don`t know what the actual tempature of the fire was at the time. Any way what we did know is that made the job of removing the rusty scale a lot easer. Also the metal was already up to a bit of a welding heat. After the welding job was completed I placed the piece in a box of zone o lite to cool off, don`t tell the inviro police that I still have Zone o-lite.The process was very simple and with out formula,cook,clean,weld,assemble,play with it. |
   
axtion_jim
Advanced Member Username: axtion_jim
Post Number: 36 Registered: 11-2010
| Posted on Tuesday, April 16, 2013 - 12:18 am: |
|
Purchased a Duncan EA-716 Kiln today. Rated for 2714 degrees fahreneit, that should do the trick on the salt. All I have to do now is wire the kiln for the 240 volt single phase. |
   
robert
Senior Member Username: robert
Post Number: 548 Registered: 07-2003
| Posted on Tuesday, April 16, 2013 - 01:34 am: |
|
Funny you say that; I just bought a kiln too! After I do my cylinders it can go to the next guy. Use outside on a VERY windy day! |
   
robert
Senior Member Username: robert
Post Number: 549 Registered: 07-2003
| Posted on Tuesday, April 16, 2013 - 01:54 am: |
|
Funny you say that; I just bought a kiln too! After I do my cylinders it can go to the next guy. Use outside on a VERY windy day! |
   
richardday
Senior Member Username: richardday
Post Number: 1056 Registered: 11-2003
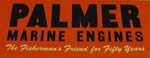
| Posted on Tuesday, April 16, 2013 - 03:11 pm: |
|
When I see super high temperatures I wonder how much warping will occur in the casting. I would urge a little practice on junk hollow castings. It is one thing to drive the salt out of the iron but if you are not careful you can warp the casting so it is permanently damaged. Seems to me the objective is to get the rust to break loose and at the same time not destroy the casting. |
   
robert
Senior Member Username: robert
Post Number: 552 Registered: 07-2003
| Posted on Friday, April 19, 2013 - 02:16 am: |
|
One thing I wonder about the heat method vs. electrolysis is that the latter method is supposed to restore some strength to the treated iron if I remember rightly? Could that effect be achieved by doing electrolysis after the heat treatment has burned out all paint, oil residues etc. that might interfere with the electrolysis? |
   
jb_castagnos
Senior Member Username: jb_castagnos
Post Number: 791 Registered: 07-2002
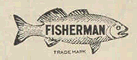
| Posted on Friday, April 19, 2013 - 09:19 pm: |
|
Electrolysis travels "line of sight" or shortest path. If you put a large cylinder in the tank, the external parts are closest to the return path, there's going to be little flow from the interior of the jacket. Painting the exterior would help insulate it and make it draw from the interior. I think you could put a perforated cover over a rod and slip it into the jacket, the cover would keep it from grounding and allow you to clean the inside of the cylinder. |
   
marks
Senior Member Username: marks
Post Number: 149 Registered: 03-2002
| Posted on Saturday, April 20, 2013 - 05:33 pm: |
|
For electrolysis I thread a piece of stainless wire through the water jacket which is inside a piece of clear plastic tube (from the aquarium shop). The tube has holes drilled through it every half inch or so, from one side to the other. Sometimes it is necessary to drill holes in the jacket to get enough access. These are easily plugged when done - tap, screw a bolt with a dab of epoxy and cut it off. In terms of heat I find that cherry red (in the shade in daylight) works fine. I have pieces which were in poor condition done 10 years ago and they are going fine. Cheers, Mark S. |
   
davey1000
Member Username: davey1000
Post Number: 5 Registered: 12-2010
| Posted on Monday, April 07, 2014 - 04:29 pm: |
|
I have had some success with cylinder blocks from the "British Seagull" outboard motors. These are two-cycle motors which are raw water cooled. A lot of people despise these motors but after fifty years of abuse and neglect how can they be expected to work properly? One needs to remove the block from the crankcase then remove the cylinder head which is marked "Do Not Remove". Usually all the water passages will be choked solid with rust. A drill press fitted with a masonry drill can be used initially but use the type with a round shank and don't have the drill chuck or the pulley belts too tight. A Dremel fitted with grindstones can also be useful. Formic acid sold as kettle descaler does remove rust if left overnight but the end result is rather messy. One article that I read that was written in the 1920s advised using Hydrofluoric Acid as allegedly it dissolves rust whilst ignoring metal but HF is such a dangerous chemical that other ways need to be investigated. Phosphoric Acid perhaps? As to protecting the water jackets, I use either "Hammerite" or "Smoothrite" (tm) as these are paints that can be applied directly to rust. Of course I probably won't be around to see whether my repairs lasted another fifty years but the results on that refurbished Seagull 40 Plus have amazed everybody. OK its a "Gold Top" (The Wipac ignition version) so it starts on the first, second or third pull. The improved cooling means that it can run for as long as the fuel lasts and there is no cutting out or stalling caused by excess heat. The bad reputation is caused by silly people trying to use stale fuel in 50 year old motors with rusted-up water jackets and guess what? The motors won't work! It's not rocket science! |
   
davey1000
Member Username: davey1000
Post Number: 6 Registered: 12-2010
| Posted on Monday, April 07, 2014 - 04:51 pm: |
|
PS A lot of UK museums and government departments use "Fertan". AFAIK this is based on tannic acid. It turns the rust to a dark blue colour but it will also stain ones hands and clothing. As chemicals go this one seems fairly safe to use. After the metal has been treated one washes-off the un-reacted Fertan several hours later. The metal is then dried and painted. |
   
ernie
Senior Member Username: ernie
Post Number: 1814 Registered: 01-2002
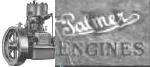
| Posted on Tuesday, April 08, 2014 - 05:12 pm: |
|
I am going to try some POR 15 paint in the next few days. POR is paint over rust. http://www.por15.com/ |
   
bpineo
Member Username: bpineo
Post Number: 24 Registered: 05-2008
| Posted on Tuesday, April 15, 2014 - 05:34 pm: |
|
Hey Ernie. Brandon here. I have tried the por-15, and I must say that the "Metal prep etch" that they sell as a companion product is very good. I tried the paint without the prep and it did peal after a winter of use. Bought the prep-etch solution and the paint never pealed again. It's the only part of my car that did not rust! |