Fairbanks Morse Marine Engine |
Author |
Message |
   
richarddurgee
| Posted on Sunday, November 23, 2003 - 05:48 pm: |
|
Just took this one off bench, its ready to start up, I'm sure it hasn't run in many decades. Had the most difficult stuck piston in it i have ever dealt with, once piston was out, cyl was honed, bead blasted piston and rings, has great compresion and excellent bounce back, should be a strong running little eng ! All original except spark plug and paint ! 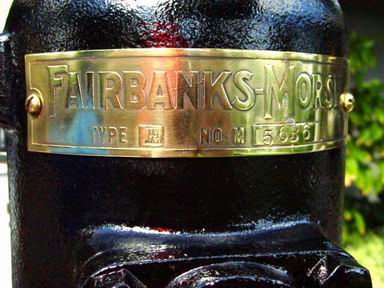 |
   
Richard Day
| Posted on Sunday, November 23, 2003 - 08:55 pm: |
|
Outstanding job. |
   
richarddurgee
| Posted on Sunday, November 23, 2003 - 10:14 pm: |
|
Thanks Dick, You may remember that eng, it sat on your shelf several years, turned out better than pics, some days the digital camera and me don't get along as good as other days, maybe the Fla sun and the black enamel ??? |
   
Richard Day
| Posted on Monday, November 24, 2003 - 08:15 pm: |
|
Yes I remember. I did the hardest part which was to move the piston the first 1/4". Did you use the hydraulic method as I use where you push it out as far as you can and then push it back until you can extract the piston from the bore? |
   
richarddurgee
| Posted on Monday, November 24, 2003 - 09:46 pm: |
|
Dick First attempts to move the piston by hydraulic pressure didn't work, so I made a puller to go across cylinder base to wrist pin to pull it and hydraulic method to push at same time but also used heat several times in between push and pull attempts, finally after about 2 months the piston finally moved. Whats interesting is the condition of the bore, put a flex hone in it and mic'ed it, not a spot or any aprecciable wear, piston the same, rings had a few spots on them but very usable.Seems to be a very well made little eng. Thanks |
   
Richard Day
| Posted on Tuesday, November 25, 2003 - 05:03 pm: |
|
Well I am glad you got it out without damage. My experience with pulling was fatal on a Lockwood Ash. Had not learned about the hydraulic method at that time. I am puzzeled because I clearly moved it hydraulicly about 1/4" but then set it aside as another job to do. Looks like you did a nice repair job on the brass tag. |
   
Tom Stranko
| Posted on Monday, December 01, 2003 - 07:33 pm: |
|
Great looking engine Richard. Where did you apply the heat exactly? (propane, acetelyne?) |
   
J.B. Castagnos
| Posted on Monday, December 01, 2003 - 07:55 pm: |
|
Good job on the engine Richard. Whenever possible I try to press a stuck piston inward a little to break it loose before trying to pull it out. I use a piece of pipe that fits on the skirt of the piston, long enough to go past the rod. Set it up in the press and apply pressure. If nothing gives before you get uncomfortable with the pressure get the acetylene torch with a large heating tip and apply heat around the cylinder, into the water jacket if the piston is deep. It's suprising how quick the piston will move when the heat is applied, I've seen several pop loose before you make a round with the torch. |
   
richarddurgee
| Posted on Monday, December 01, 2003 - 10:20 pm: |
|
Tom With this eng I first tried hydraulic method with grease gun, went to limit of what I felt might cave piston in.I then made a puller over wrist pin and put a good pressure on it and tried hydraulic at same time. Then put cyl in a iron pot and built a fire of wood and let it heat up and cool down twice, puller pressure still on. Then put cyl upside down and put fluid in to fill piston up and let it burn for most of a day. Lastly used acetelene torch to heat cyl with puller and got movement ! J.B. I didn't try pushing it deeper in cyl but that sounds good, How do you support cyl in press? always fear crushing water jacket. Thanks Richard |
   
Richard Day
| Posted on Tuesday, December 02, 2003 - 08:48 pm: |
|
Richard, I take a piece of 1" steel plate set a strip of aluminum about 1"+ wide long enough to circle the cylinder head with about 1/2"-1"clearance all around. Hold it in place with a few bits of steel Melt lead and pour in about a 1/4" thick pad. Let it solidify then suspend the cylinder just clearing the lead so any boss or plug will not touch the lead. Once that is done heat enough lead to fill the dam at least to the upper portion of the cylinder enough so the radius of the head will be totally immersed in molten lead but not so high that you will trap the head by the straight side of the cylinder. I plug any threaded holes in the head so the lead will not flow into the water jacket, cylinder or priming cup appertures. As soon as the lead solidifies you are then ready to press the piston in with assurance that the stress will be over the entire head of the cylinder and no pressure points will be developed. The reason for the first pour is to keep the dam from walking around and leaking most of the lead under the dam. The hieght of the dam really depends on the radius of the head. The second pour must be made in one pass if it is to succeed. If it doesn't break it out and start over. Like in pouring babbit take the chill off the cylinder head so the lead doesn't cool too quickly |
   
J.B. Castagnos
| Posted on Tuesday, December 02, 2003 - 09:46 pm: |
|
I''ve looked at several freeze damaged cylinders and the spark plug area is usually about a 2" casting to the combustion chamber. I support the cylinder below the plug area. Apply as much pressure as you are comfortable with and start heating. I wouldn't use the grease gun method until I've seen a piston move. I had to sleeve a blown out cylinder for a friend, the wall gave out before the grease moved the piston. I'm sure the cast cylinder is much stronger in compression in the press than it is in expansion by the grease. |
   
richarddurgee
| Posted on Saturday, December 06, 2003 - 08:23 pm: |
|
The next stuck piston I deal with think I'll see if it has plenty of iron around head,if so I'll do as J.B. does and press it in. If it looks thin or a salt used eng I'll pour the lead around it as Dick suggested. I Worked in a small foundry as a teenager so pouring the lead is not a problem to do. have learned to go slowly with any process of getting stuck iron apart, took along time to get that stuck, may take some time to get unstuck without breaking something ? Thanks for replies Richard |
   
Josiah Hanna
| Posted on Thursday, January 29, 2004 - 07:26 pm: |
|
Do you know the horsepower? |
   
richarddurgee
| Posted on Thursday, January 29, 2004 - 07:44 pm: |
|
The eng pictured above is a Type " E " 3 1/2 HP. |
|
|
|
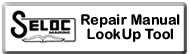

|