Author |
Message |
   
Ernie
| Posted on Wednesday, January 23, 2002 - 12:20 pm: |
|
Gents, See attached pics. Note on the top the guck appears crumbly. As you go lower the guck gets harder. Ernie.
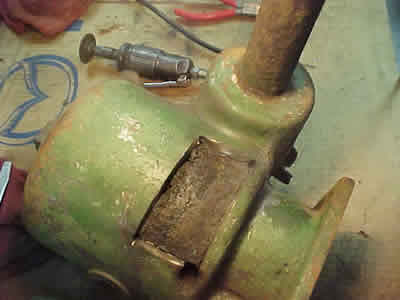 |
   
Joe
| Posted on Wednesday, January 23, 2002 - 02:52 pm: |
|
Looks like you have lots of wall thickness left. Most of my engines are/were saltwater cooled and I know the problem well. How do you close it up? I have had success using J B Weld. Is that an Acadia?? |
   
ernie
| Posted on Wednesday, January 23, 2002 - 03:34 pm: |
|
Yes this is a 3 hp Acadia. This is kind of an expirement. I have a 3 hp Acadia that has a plugged water jacket. I can't run ot for long as it gets pretty hot. This cylinder appeared good, however it was plugged worse than my running one. I coulnd't even get water through it at all. So the reason for the cutting was to see if I could clean it out. I now have cut a similar window in the front and also cut out the bottom of the exhaust elbow. It is now clean enough to run cool. I will most likely use JB weld. Im my opinion there is none better. However I just got some stainless wire for my MIG welder. I may try that. I will let you know. Have a good one Ernie |
   
Joe
| Posted on Wednesday, January 23, 2002 - 08:13 pm: |
|
Ernie, your pictures are proof that the Atlantic salt water is just as bad as the blue Pacific salt water. I have had to use cold chisels to bust stuff out as there is no way a small hole and coat hanger will work in these cases. Can I suggest that when you cut another window, try cutting opposite sides at an angle so the window goes back into place as a plug. The thickness of the epoxy in the joints will bring the window back to flush. The reason I like epoxy over welding is there are no local stresses set up from heat. The outer wall of the water jacket does not require strength, all it does is keep the water in.....regards.....Joe out west. |
   
ernie
| Posted on Thursday, January 24, 2002 - 05:45 pm: |
|
Joe, I have about 99% of the water jacket clean. You are right It takes chisel and hammer to get the rust out. I also use masonry bits in some areas. I have done many engines. This one is kind of an expirement. I have had real good luck with stainless wire in my MIG on other cast iron stuff. I only weld about 1/4 inch at a time. I then peen it till cool. I never let any area get hotter than I can lay my hand on. (except right after the short weld) I suspect the high nickel content helps the stainless stick. However I may still use JB Weld. I know it always works. I make supports and dams out od styrofoam inside the water jacket to support the piece that I cut out, also to keep the JB from sagging into the water jacket. Once the cylinder is complete I just pour in some gasoline. styrofoam is instantly gone. I then mix up some real watery zinc chromate primer and pour it into the water jacket. It will drain out in a day or so. This seems to stay put and keep the air away from the salty iron once it is dry. |
   
Joe
| Posted on Thursday, January 24, 2002 - 10:52 pm: |
|
The styrofoam trick is a good tip, thanks for that. I would like to share an experience that I had which might be of benefit to others who mess about with marine engines that have been salt water cooled. I came to own some old 4 cycle engines that had spent many years of retirement in sheds and basements and so on. The cylinders and heads and manifolds (water jacketed parts) all seemed to be in good shape, no cracks or rust streaks etc. I parted the engines that where all in need of a good cleanup. I hot tanked (caustic) everything and then glass beaded some of the bits and pieces, did a spray wash and when dry primed the metal and then painted. The engines looked great. Some months later most of the water jackets were split from interior rust heaves. What happened?? These engines were in fine shape until I cleaned them. It had to be the hot tank that catalized the rusting process. Lesson, do not hot tank water jacketed parts or find some way to neutralize the parts after. Question, how would you do this? I thought of heating the parts in a bucket of hot oil for a while then I thought, would I be able to paint over oil impregnated parts. Have you had any experience with this??............. |
   
miro
| Posted on Saturday, January 26, 2002 - 08:20 am: |
|
Guys, doesn't this sort of major surgery on the waterjacket cause a significant reduction in the strength of the cylinder. On my engine, the 2 cycle ports occupy so much of the circumference that the only thing holding the top of the cuylinder to the bottom really is the water jacket. The cast webs between the ports are about 3/8 in by 3/8 - practically nothing and the ports go almost all the way around . I have a Gray 4 in bore x 4 in stroke. miro |
   
Robert Holcomb
| Posted on Saturday, January 26, 2002 - 03:51 pm: |
|
Well might as well create a ruckess here,i choose to braze the water jackets,the reasons behind this is that arc welding creates a stress area around the weld causing more cracks ,peening is often mentioned to relieve the stresses as the part cools.also paint doesn`t stick very well to nickel rod. also nickel rod is hard to rework,it becomes very tough and hard...where brazing is controlled to 700-900 degrees verses several thousand for arc what i do is use a weed burner to bring the part up to temp as evenly as possible then braze it then i use an old propane bbq to lower the temp gradually over a few hours,has worked fine for me over the years,also i hold the temp at 5-600 for at least an hour to aneal the material and stress relieve it,cast iron with age crystalizes and that is a big problem,lots of older machinery has been removed from service over this problem,holding at high temp is reported to improve the grain structure,an old blacksmith my dad knew would build a fire around the casting to be fixed and then braze it and then put it back in the coals coverd up with ash to let cool,pot ash is a wonderful tool,coke is still used in the manufacturing of iron.in some of the old books there is reference to aging a casting for improved results. For me i will braze,i just happens to work for me here is what i do preheat part in old bbq or weed burner braze part keeping part hot with weed burner cool down and anneal in old bbq This is just my opinion bob.... |
   
Geoff Archer
| Posted on Sunday, January 27, 2002 - 10:38 pm: |
|
Hi Folks I'm in the process of restoring a Blaxland Master Pup 2 stroke single (Cast Iron)cylinder marine engine. She has a few cracks in the water jacket which allow water to seep through and a few others which I'm not sure if they are cracks or casting imperfections. What do you think is the best way to repair these cracks. Iwas going to use a CI (Nickel)repair rod but are there any other alternatives/ suggestions (ie preheating etc) that work , and how do you stop further cracks/deterioration in the water jacket. Thanks for any advice |
   
Tom Stranko
| Posted on Tuesday, January 29, 2002 - 07:10 pm: |
|
I have had to clean out water jackets clogged by salt water rust and the hydrochloric acid you can buy from a hardware store (as muriatic acid) works great. The acid is used to etch concrete before patching. The same acid is sold to adjust swimming pool PH. Now, if you're a stupid person (as Jeff Foxworthy?? says) don't go near this stuff. But if you can do it OUTSIDE !! and don't get it on your skin or clothes and don't look into the water jacket entrances while this is going on you will be ok. The worst that could happen is you could splash it on your eyes which would be the end. That said, I will say I have used gallons of the acid with no bad effects. Remove all parts from the cylinder and plug the water holes. I just put the cylinder in a large plastic tub and pour in a bit of acid. If there is a lot or calcium (lime etc) from hard water it will be very active at first. You will probably have to let the acid soak for hours then (put on some rubber gloves and heavy ones) pour the spent acid out into another plastic bucket. I generally use a garden hose to wash out any "stuff" loostened but not disolved by the acid. Then refill and wait etc. This takes a day or more depending. Have to admit I have not tried it on such a bad looking cylinder as that Acadia but hey, this is supposed to be something to take up your free time. I generally use Hitemp 5min epoxy by Loktite to patch the crack (sandblast first) You can use a hi speed grinder to smooth out the Loktite epoxy with ease (does not smear when hot). I have been using a product called POR15 to seal up the cylinder insides and it seems to be ok. Good at rust prevention and does not seem to effect heat transfer. Anyway, my 2cents |
   
peterogborne
| Posted on Thursday, February 07, 2002 - 09:35 am: |
|
Tom ,I have done the same acid cleaning treatment but I do neutralise the effect of the acid by washing the cylinder in Bi - Carb of soda .I can only recomend the method Ernie uses ,I have done the same many times . |
   
Tom Stranko
| Posted on Thursday, February 07, 2002 - 07:39 pm: |
|
Yes, you have to neutralize the acid with something like lye water or bi-carb of soda (is that like baking soda?) The old car restoration magazines I have say to put formaldehyde in to convert the acid somehow. I got some from Chemtech here and was aware it was now a "carcinagen" per the feds but the guy there laughed and said "just don't drink it" |
   
peter ogborne
| Posted on Friday, February 08, 2002 - 09:00 am: |
|
Yes Tom it is the same ......I pinch it from my wife's pantry . Talking about cleaning .......some advocate the use of Citric acid to remove rust . In talking to our local marine museum they say to exercise caution as it can cause stress fractures in castings . Personally I have tried it and found it most inefective ,I prefer the good old molasses bath . I find puting a leghth of frayed steel hand brake cable in the chuck of an electric drill gets into all those hard to get at water jacket spaces . |
|
|
|
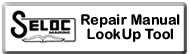

|