Author |
Message |
   
rdomoe
New member Username: rdomoe
Post Number: 1 Registered: 11-2009
| Posted on Sunday, November 15, 2009 - 10:49 am: |
|
I am seriously considering purchasing a Gray 8 HP "T" engine on a workhorse base. The flywheel has several radial cracks and the hub also has thru cracking around it. This engine has not been run by the current owner but has been meticulously disassembled, cleaned and repaired as necessary. The original head is also missing but replacement has been fabricated. Some comments on this issue would be greatly appreciated!}} |
   
marks
Senior Member Username: marks
Post Number: 119 Registered: 03-2002
| Posted on Sunday, November 15, 2009 - 07:26 pm: |
|
I personally wouldn't run an engine with a cracked flywheel. The energy stored in a rotating flywheel of any mass is significant. If it were to come apart it could cause serious injury or death. Also I personally would not attempt to repair a flywheel, I either wait till a good one turns up or use a good flywheel from another engine which can be "adapted" to suit. The issue with repairs, whilst they might be possible depending on the situation, is that the engine will most likely end up with somebody else in the future. They may not be aware of the repairs and the potential of failure and resulting consequences. So my opinion is that cracked flywheels should not be run nor repaired. Mark S. |
   
frank_petran
Senior Member Username: frank_petran
Post Number: 70 Registered: 05-2009
| Posted on Sunday, November 15, 2009 - 07:52 pm: |
|
I had a new flywheel cast and machined for the Gray have. I borrowed one and used that as a pattern. I then had it machined. I had to take it to a large machine shop that could swing a 16 inch, 65 pound flywheel as most small shops do not have that capacity. Also because it is a tapered shaft with a keyway a large shop with that expertise would have a lot of experience with that type of machining. I sent the engine along so that they could fit the flywheel porperly. The casting cost about $130 and the machining about $250. Not bad for an engine that runs. |
   
rdomoe
New member Username: rdomoe
Post Number: 2 Registered: 11-2009
| Posted on Sunday, November 15, 2009 - 08:42 pm: |
|
Thanks for the feed back, that was my spin on this engine also. I have the capability to turn 20" diameter in my shop. If I purchase this engine I WILL make a new flywheel. Thanks again |
   
miro
Senior Member Username: miro
Post Number: 410 Registered: 11-2001
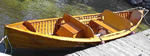
| Posted on Sunday, November 15, 2009 - 08:46 pm: |
|
The cracked flywheel is a disaster waiting to happen. Esecially the cracks at the hub. Even at a low speed - say 300 rpm, the damage to you and anyone close by could be really really bad. Get the present owner to understand the danger he or she is in. Or failing that, buy the engine at a discount and NEVER run it. Miro |
   
richardday
Senior Member Username: richardday
Post Number: 829 Registered: 11-2003
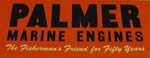
| Posted on Monday, November 16, 2009 - 08:15 am: |
|
Cutting a tapered keyway seems to me to require a special machine where the flywheel can be rocked to the same angle as the tapered key. I think Bob Price mentioned that problem several years back. I wonder how many machine shops have that sort of machine today? |
   
kerrigan
Advanced Member Username: kerrigan
Post Number: 35 Registered: 06-2008
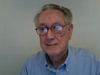
| Posted on Monday, November 16, 2009 - 09:09 am: |
|
Coupling manufacturers such as Fast's, Falk, Thomas and those who supply and use shaft couplings frequently use tapered fits between the shaft and coupling. Contact a shop that repairs industrial pumps and compressors. |
   
frank_petran
Senior Member Username: frank_petran
Post Number: 72 Registered: 05-2009
| Posted on Monday, November 16, 2009 - 12:27 pm: |
|
Checked with my machine shop, Kempsmith Machine of Milwaukee did the work. Dad said that they set the compound tool holder at the correct angle and backed the cutting tool out. For a perfect fit the taper would then be sent to the grinding area for finish work |
   
thomas
Senior Member Username: thomas
Post Number: 349 Registered: 07-2002

| Posted on Monday, November 16, 2009 - 09:35 pm: |
|
Just a test. A member said he was unable to post to this thread for some reason. Tom |
   
thomas
Senior Member Username: thomas
Post Number: 350 Registered: 07-2002

| Posted on Monday, November 16, 2009 - 09:48 pm: |
|
I have an inboard with a replacement flywheel made by an expert machinist. He made it from a "slice" of a 14" or 16" cast iron bar that he bought on the regular metal stock market. He then turned the "slice" to match the original wheel. It's a perfect job. You don't have to always go the foundry route. (but I agree about the real danger in using the cracked wheel for anything but a door stop) T |
   
frank_petran
Senior Member Username: frank_petran
Post Number: 73 Registered: 05-2009
| Posted on Monday, November 16, 2009 - 10:16 pm: |
|
The main reason for having a cast flywheel is that my engine is a Gray and the Gray name and Detroit MI is cast in raised lettering on it. Just looks good. |
   
raa
Member Username: raa
Post Number: 6 Registered: 02-2007
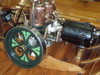
| Posted on Monday, November 16, 2009 - 11:14 pm: |
|
One easy to get keys cut in a tapered bore is to take the Minute Man broach sleeve for say 1.5" bore and lay it in the bore of the flywheel which might have a bore of say 1.75". Let the sleeve extend thru the bore a little, then pack the stuff which is used to dam around shafts when pouring babbit. Pack just around the sleeve and flywheel bore at the bottom. Then with the flywheel horizontal heat up some Woods metal or Ceroloy which melts at 150 degrees or so and pour it into the flywheel bore. This will lock the sleeve in nicely. Now support the sleeve in the arbor press with anything which will alow the broach to pass thru. The flywheel will have to be supported because it will be at some angle. Proceed to broach in the usual way and melt the ceroloy out with a heat gun. I did a small job like this in under 15 min. |