Author |
Message |
   
keith
Senior Member Username: keith
Post Number: 376 Registered: 02-2002
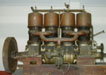
| Posted on Wednesday, February 06, 2013 - 11:04 am: |
|
I recently picked up an engine that has cracks around the bottom of the water jacket. The engine has been stored dry for many years. The cracks appear like they could be salt cracks in that there is some swelling of the crack. The water jacket is open to the (bottom) drain area and is not caked. I can, with a wire, pull out flakes of rust. I put some flakes in distilled water and checked after a week with a salinity gage and there was no indication of salt. Does that mean anything? I am leaning to think the cracks are a factor of engine use after a freeze crack and the constant weeping which would cause a rust swell in the crack. It doesn�t make sense for the water jacket to be open if it were salt rust. This is a very desirable engine and I want to do the right thing. I am concerned with doing a high heat process because of the potential for warping. Thoughts? |
   
richarddurgee
Senior Member Username: richarddurgee
Post Number: 2976 Registered: 11-2001
| Posted on Wednesday, February 06, 2013 - 03:38 pm: |
|
* Keith I second your concern with the high heat process and warpage etc ! My opinion only here, I also don't feel right with using epoxys etc they just don't seem like a quality long term repair especially with some of these high end old engines that will be around for many more decades. Owning and operating an auto/truck Radiator & A/c shop for 40 yrs i have soldered, silver soldered and brazed most metals that hold water or refrigerant including manifolds and blocks. My choice of repair is open flame acetelyne brazing for these old marine water jacket cracks, I stop drill then use a hand grinder with a metal cutting blade ( no grinding wheels they plug up the metal pores)making a slight vee shape, use Johnsons brazing flux and brazing rod,with right heat and flux you can feel the braze take to the cast iron, pre heat I just pass the torch over the localised area it isn't to important, after brazing it in a shallow wood box with sand in it that lets me move the material in any direction I cover it with a welding blanket and let it cool over night. Have done many this way and no problems some old engs are now 20 yrs since brazing and are fine were they were brazed. If chunks of cast iron are broken away That's Geoge Coates dept ! Geo I believe repairs cracks with open flame and uses cast iron rods and flux ? maybe he will enlighten us about his magic touch ? I have not tried this yet but will next repair I get into-- has anyone used it ??? http://www.castaloy.com/castironrepair.htm Because of the temerature involved this would be considered soldering, if the flux is right and the filler metal good it should be a great way to repair water jacket cracks ? Looking foreward to all opinions !! * |
   
jb_castagnos
Senior Member Username: jb_castagnos
Post Number: 761 Registered: 07-2002
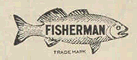
| Posted on Wednesday, February 06, 2013 - 09:12 pm: |
|
Keith, the salt damaged motors I've seen have been solid rust in the jacket, almost as hard as cast iron. |
   
gebaker
Member Username: gebaker
Post Number: 4 Registered: 09-2012
| Posted on Thursday, February 07, 2013 - 12:20 am: |
|
I appreciate everything above that you all have mentioned. However, I have had great experience with authentic cast iron welding. It isn't something you can do yourself- but it is a permanent solution. I have had personal experience with several castings sent to Crow's Cast Metal Welding in WI www.castmetalwelding.com/. They have the equipment to bring the metal to the correct temp, weld it, temper it or whatever it is called, then cool as appropriate- at reasonable prices. If you want a permanent solution to be worry and forget- perhaps you can give them a call. I had a 1933 Universal with two cast iron connectors that had to be reconstructed with only 50% original metal there- and a significant head crack that were done superbly. Too, they appreciate the historic nature and visual appearance of their work. While I prefer to do my work myself- I wouldn't hesitate to contact them on this project. Others in in their area can attest to their work from the Bob Speltz chapter of the ACBS- and they are friendly and nice too. I agree about the water jacket too- I have an Albin 029 Combi that had so much buildup from saltwater in the jacket that it was hard to differentiate it from the cast iron block. Gary |
   
searcher
Senior Member Username: searcher
Post Number: 548 Registered: 10-2004
| Posted on Thursday, February 07, 2013 - 12:53 am: |
|
At least 75% of the marine engines I see locally have been used in salt or at least brackish water. Most have cracks in the water jackets. The corrosion deposits I see in the water jackets range from tightly packed shaley iron oxides to deposits that resemble portland cement (but are much harder and tougher than portland cement). My impression is that the portland cement like deposits are a combination of mud and iron decomposition products, i.e., the engine was used in a shallow area and mud got sucked into and deposited in the cooling system. Those cement like deposits are refractory to the extent that 1000 degrees fahrenheit is not enough to decompose them. I suppose those deposits are similar to the cement/iron filings grout we used to lock in the bolts that held mine hoists and compressors to their foundations (50 years ago, anyway). Generally, but not always, cracks in cast iron due to salt water have distinctive features. It might be helpful if you could post a good clear photo of the cracks. |
   
keith
Senior Member Username: keith
Post Number: 377 Registered: 02-2002
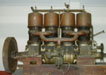
| Posted on Thursday, February 07, 2013 - 11:11 am: |
|
I am attaching pictures.
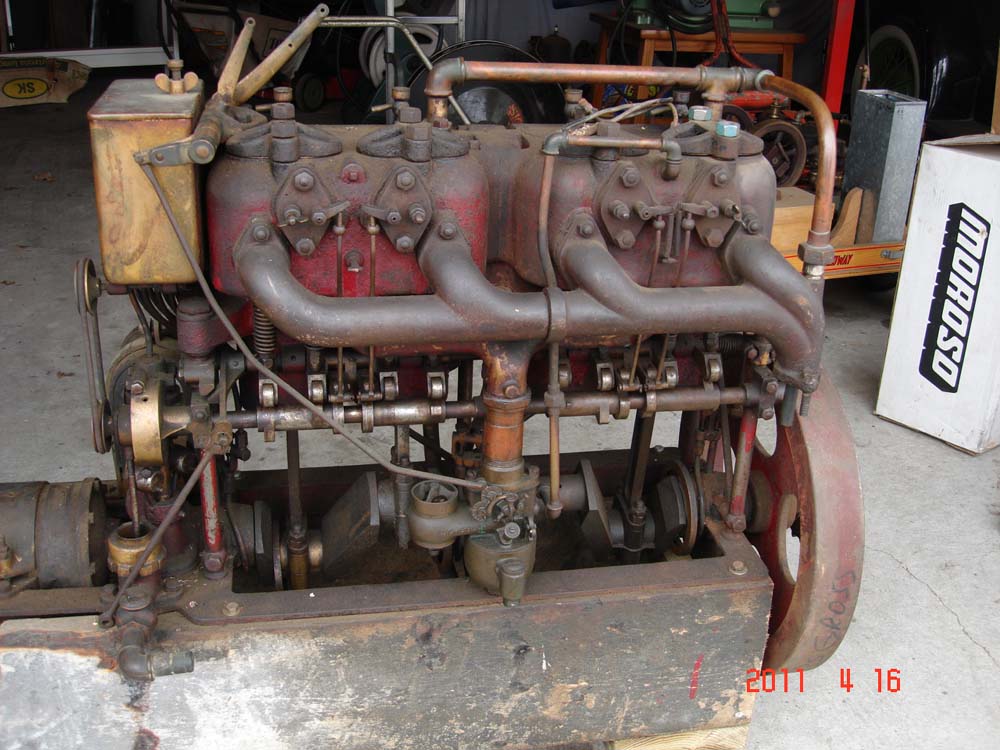 |
   
keith
Senior Member Username: keith
Post Number: 378 Registered: 02-2002
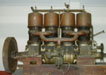
| Posted on Thursday, February 07, 2013 - 11:18 am: |
|
One more picture.
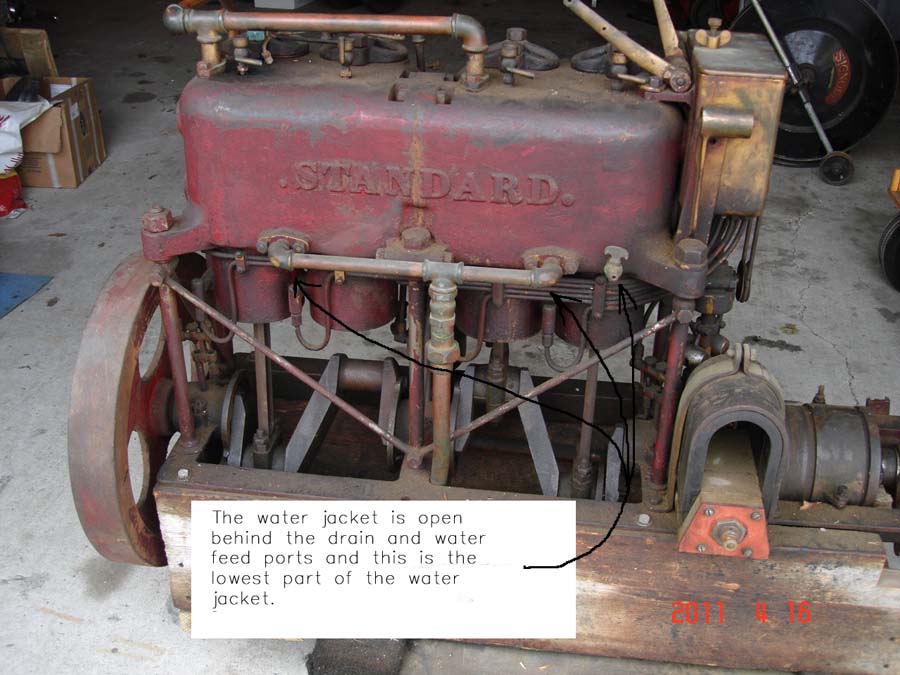 |
   
richarddurgee
Senior Member Username: richarddurgee
Post Number: 2978 Registered: 11-2001
| Posted on Thursday, February 07, 2013 - 01:10 pm: |
|
* What a great old marine engine I brightened up the photos a bit
This well over 100 yr old Lathrop came to me with the crack repair patch, I took the head off and the jacket inside was surface redish with flakes that blew out with air no sediment etc, it had a minor 2 inch crack that was visible but not wet wth anti freeze after filling it and keeping an eye on it for a month or so --- lesson learned is that hidden in storage for almost two yrs the crack did open enough to let the anti freeze drain out and things went down hill fast the crack now is open and about 8 inches long. If I can't repair these situations right away ( I have a few more similar) I have cleaned the cracks and silicone sealed them temporarily to get the antifreeze back in them. My take on these engs is that they had salt water exposure at some time in their life but maybe spent most of it in fresh water ??
* |
   
george_iv
Senior Member Username: george_iv
Post Number: 91 Registered: 07-2003

| Posted on Thursday, February 07, 2013 - 02:36 pm: |
|
Some pictures of known salt water cracks and issues. Some with concretions and some without.
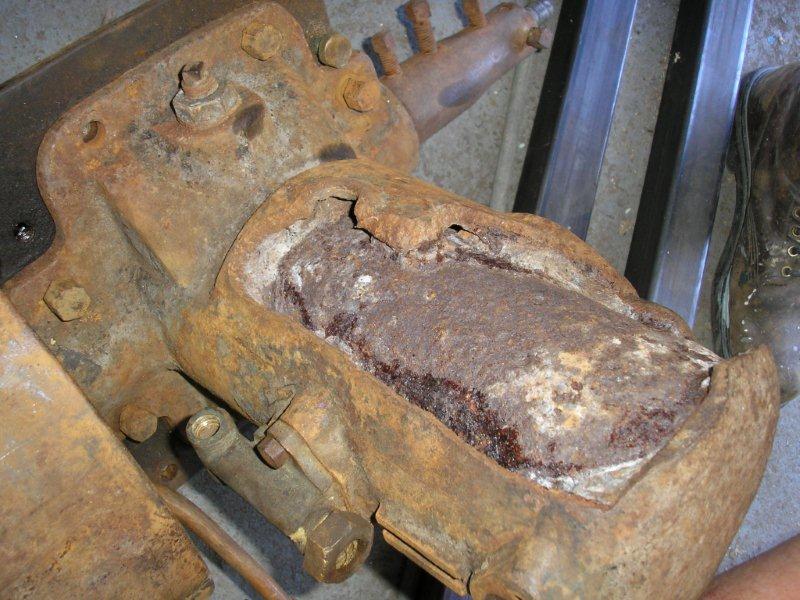 |
   
searcher
Senior Member Username: searcher
Post Number: 549 Registered: 10-2004
| Posted on Thursday, February 07, 2013 - 04:20 pm: |
|
Here are some additional photos of saltwater cracks and freshwater frost cracks. The following comments are from my own experience. I expect somebody can come up with an example that contradicts every observation I offer. That's great because it advances knowledge on the subject. Saltwater cracks often run parallel with the circumference of the very lower part of the water jacket. If higher up on the water jacket, the cracks tend to radiate from a common point/points. The cracks higher up on the water jacket tend to be 'ragged' and comparatively short until the problem has advanced. Multicolored stains and deposits are common along the cracks. Freshwater frost cracks tend to run parallel to the long axis of a cylinder. The frost cracks are often long, fairly linear, and lack the 'ragged' look of salt water cracks. Generally, I don't see strong multicolored deposits along frost cracks.
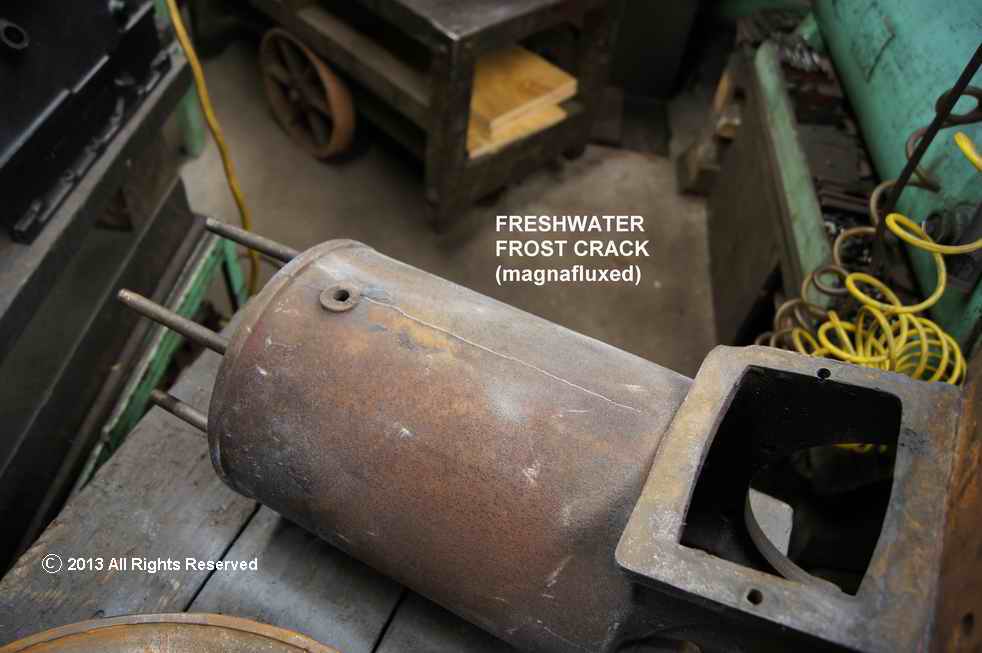 |
   
jb_castagnos
Senior Member Username: jb_castagnos
Post Number: 762 Registered: 07-2002
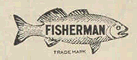
| Posted on Thursday, February 07, 2013 - 10:51 pm: |
|
That's a fine engine Keith, do you have the missing piston? The ignitors appear to operate off of the cam with no snap action, looks like the ignitor lobes drop off fast. |
   
keith
Senior Member Username: keith
Post Number: 379 Registered: 02-2002
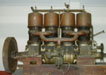
| Posted on Friday, February 08, 2013 - 09:16 am: |
|
jb, If you look close at the one picture you can see a notch in the cam lobe. It's missing one rod and piston. The bore looks good. Don't know why it was taken out. I appreciate everyone's input. It's a wonderful sharing of thoughts. The above thoughts would lead to access the cracks as salt damage. I have a hard time with the concept of a salt crack without some form of a incrustation forcing a fracture. The cylinder assembly splits in two so it should lead to good access of the water jacket. A permanent repair by brazing to a freeze crack is a no brainer. Coming up with a permanent repair to salt damage is the problem. Is there a way to chemically check for salt freeze? Thanks to all.
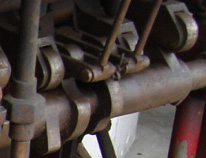 |
   
paulgray
Senior Member Username: paulgray
Post Number: 132 Registered: 05-2003
| Posted on Friday, February 08, 2013 - 01:02 pm: |
|
For what it is worth Keith, I did the baking treatment on the Castelnau block and had no problems whatsoever. After George repaired a crack similar to yours on the bottom edge of the water jacket, the jacket interior was sealed with both epoxy and thinned out rusty metal primer to get where the epoxy missed. It did allow me to tighten up some of the threaded holes in the block when the epoxy cured and was re-tapped. |
   
jb_castagnos
Senior Member Username: jb_castagnos
Post Number: 765 Registered: 07-2002
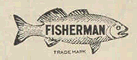
| Posted on Friday, February 08, 2013 - 07:13 pm: |
|
Keith I saw the dip in the lobes but without a trip you have to crank fast to get a decent spark. If you take a low tension coil and "make and break" the wires you can see quite a difference in the spark if you open them slowly or snap them open. This was one of the problems with piston trip systems, they always needed advance or retard to get quick enough movement to get a good spark. |