Author |
Message |
   
Searcher
Senior Member Username: searcher
Post Number: 371 Registered: 10-2004
| Posted on Tuesday, November 17, 2009 - 11:42 am: |
|
Both my pre 1911 5hp Mianus engines are missing their brass hats and one is missing the pant cuff protector over the end of the crankshaft. The pant cuff protector I do have is rather beat up (see photo below). Is there any such thing as an affordable metal spinner that could reproduce either or both pieces? How feasible/possible is it to straighten out the pant cuff protector I do have so that it looks reasonably good? What are the chances I would live long enough to learn how to satisfactorily spin brass to make them myself if necessary? Are there others with Mianus engines missing these brass parts such that we might be able to split costs in having some made?
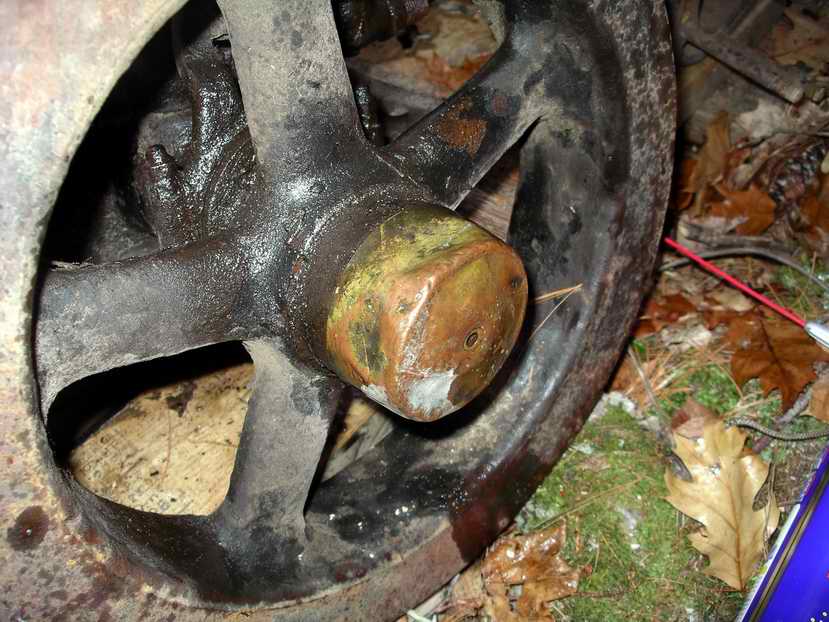 |
   
Robert B. Price
Senior Member Username: rbprice
Post Number: 265 Registered: 11-2001
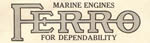
| Posted on Tuesday, November 17, 2009 - 11:56 am: |
|
Hugh - what is the wall thickness of the sleeve? You might be able to reproduce the part by finding some brass tubing @ McMaster-Carr and silver soldering and end plate to replicate the parts. The tubing could be turned with a step to fit the OD of the nose of the flywheel so you wouldn't need to bore the entire distance. Bob Price |
   
Searcher
Senior Member Username: searcher
Post Number: 372 Registered: 10-2004
| Posted on Tuesday, November 17, 2009 - 04:34 pm: |
|
Bob, I can visualize what you are describing. Ultimately it may be the best and cheapest way to go. I thought of trying to do something similar for a brass hat. Somewhere in a crate I have a 19th century blacksmith device for rolling flatstock to give it a smooth radius. It would work fine for turning a piece of flat brass into a nice ring. I could then silver solder the butt ends together. To put a cap on the ring is much more problematic. I suppose a thick piece of flat brass could be cut to size and silver soldered into the ring. By sanding the edge down, there would be a little radius though not as pronounced as the original. So, I'm not skunked yet. Thanks. |
   
Bruce Hall
Senior Member Username: bruce
Post Number: 207 Registered: 07-2002
| Posted on Tuesday, November 17, 2009 - 08:05 pm: |
|
Bob- Any chance it might be matched up to a copper sweat cap and brass plated? One could always be bushed down inside diameter for a press fit.. just a thought... |
   
Robert B. Price
Senior Member Username: rbprice
Post Number: 266 Registered: 11-2001
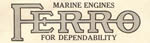
| Posted on Tuesday, November 17, 2009 - 09:09 pm: |
|
That depends entirely on the dimensions Bruce. If Hugh really has an old ring rolling tool that would be ideal to create the basic ring since the copper would be easily rolled once a good joint was made. But the copper would become quite brittle unless in was annealed after 6 or 8 passes through the machine. Seems to me that if a brass tube of the right wall thickness could be found then it, brass, is much better suited to the application than copper. Of course, it could be machined out of a brass billet so maybe it would be less expensive to just buy a piece of bar stock and give it to someone with a CNC lathe. I just purchased a piece of manganese bronze bar; 3.50 OD x 15.75 in. long: $234.00 dlvrd. to Ashfield, MA to have three indexing gears made so that gives you some idea of potential cost. |
   
Doug Kimball
Senior Member Username: doug11k
Post Number: 68 Registered: 12-2003
| Posted on Tuesday, November 17, 2009 - 10:11 pm: |
|
Could a brass pipe cap be found with dimensions close enough to allow machining to fit .... I.D. & O.D.? Not sure if you would have enough depth. |
   
Searcher
Senior Member Username: searcher
Post Number: 373 Registered: 10-2004
| Posted on Tuesday, November 17, 2009 - 10:39 pm: |
|
Maybe having the pant cuff protector cast and then machined to fit would be the way to go. It might wind up being a bit bigger than a spun one but it would look good. As to the hat, that will be a bigger problem. However, I have been eyeing the spun brass hat on a Truscott I have in the office. I am not yet convinced that I couldn't spin one after some practice and a number of failures. I caught a couple of spinning videos on the internet posted by a company in the spinning business. Fascinating to watch the metal flow over the form. |
   
Ernie
Senior Member Username: ernie
Post Number: 1103 Registered: 01-2002
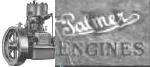
| Posted on Wednesday, November 18, 2009 - 08:03 am: |
|
If you don't mind a reddish tint just use a copper pipe test cap. They are cheap too |
   
Robert
Senior Member Username: robert
Post Number: 319 Registered: 07-2003
| Posted on Monday, December 28, 2009 - 06:04 pm: |
|
Look around your local scrap yards, you'll probably find some offcuts of round stock you can buy for the weight price: a dollar or two a pound. Have a look in the brass bins and you might find some item that could be modified or machined to simulate what you want. I would suggest a 40mm Bofors shell casing or perhaps 57mm, check your local junque shop! I'm sure you can see how one could be machined out of the bottom of a shell casing... |
   
Philip Allen Visitor
| Posted on Monday, December 28, 2009 - 08:51 pm: |
|
If you decide to go with copper, which is likely the easier route, considering availability. You may want to try a trick to give it a brass finish. When my son was in high school he came home with a brass penny of current date. The method as I recall was to polish it, put flux on it, heat it, and sprinkle or dip it in very finely divided zinc dust. Heated and wiped it appears to be brass. Of course one would want to do some experimenting on something larger than a penny first to confirm its feasibility on a larger surface. |
   
miro forest
Senior Member Username: miro
Post Number: 415 Registered: 11-2001
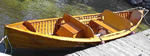
| Posted on Tuesday, December 29, 2009 - 11:13 pm: |
|
I had the same trepidation about spinning metal (brass) until I actually tried to do it. It turned out to be easier than I thought. Plan to make several versions. The real trick is to learn how to anneal the brass. I found that the mandrel ( any hardwood will be OK) will give you a near precise fit. The originals were probably spun. If you're really stuck, come down to Louisiana in March for JB's "do" and we'll figure out how to get 'er done. miro |
   
Searcher
Senior Member Username: searcher
Post Number: 400 Registered: 10-2004
| Posted on Thursday, December 31, 2009 - 03:50 pm: |
|
Miro, How much allowance does one need to build into the wood form to achieve a specific diameter in the metal, or, does the metal conform so tightly to the wood form that the outside diameter of the form will be essentially the same as the inside diameter of the finished metal object. Robert, Machining a brass shell casing might be a terrific solution for the pant cuff protector. I will look for one of the correct diameter. I do have a 5.4" dia. shell that will become sheet brass for a hat and the rest of the shell will be remade into a couple of small gas tanks. Unfortunately, some flaming idiot got cut pretty badly at a local junk yard, sued, and won. Now there isn't a junk yard in this part of the State that will let us scavange any more. There used to be some pretty neat stuff in those scarp piles. Thanks. |
   
Robert
Senior Member Username: robert
Post Number: 320 Registered: 07-2003
| Posted on Thursday, December 31, 2009 - 09:32 pm: |
|
Searcher, I think you'd find the primer hole on the casing would nicely replicate the hole in your photo above! What are the dimensions of the cuff protector? If I see a suitable casing in my travels I'll measure it up. As for the scrap yards... Typical litigeous cr*p eh? Same thing happened around here recently, a woman 'strained' herself pulling something out of a scrap bin and then had the cheek to complain to the municipality. Result: no one gets to save anything from the shredder. That's the world we live in. |
   
Searcher
Senior Member Username: searcher
Post Number: 402 Registered: 10-2004
| Posted on Sunday, January 03, 2010 - 09:00 pm: |
|
Robert, The outside diameter of that pant cuff protector would be 3 3/32". Thanks for keeping an eye out for a shell casing. |
   
Robert
Senior Member Username: robert
Post Number: 323 Registered: 07-2003
| Posted on Monday, January 04, 2010 - 12:43 am: |
|
Searcher, if memory serves, a 40mm Bofors casing is going to be tad big, but I could be wrong...maybe the 37mm antitank gun? Try Collector's Source, they have quite a selection in stock. |
   
Searcher
Senior Member Username: searcher
Post Number: 524 Registered: 10-2004
| Posted on Monday, March 26, 2012 - 04:27 pm: |
|
This Mianus ad from December 10, 1912 is about as informative as engines ads get. It doesn't print well at the OME 100K limit but it does print well at 3.3MB. If anyone wants to print it at 3.3MB, email me and I will send the file to you.
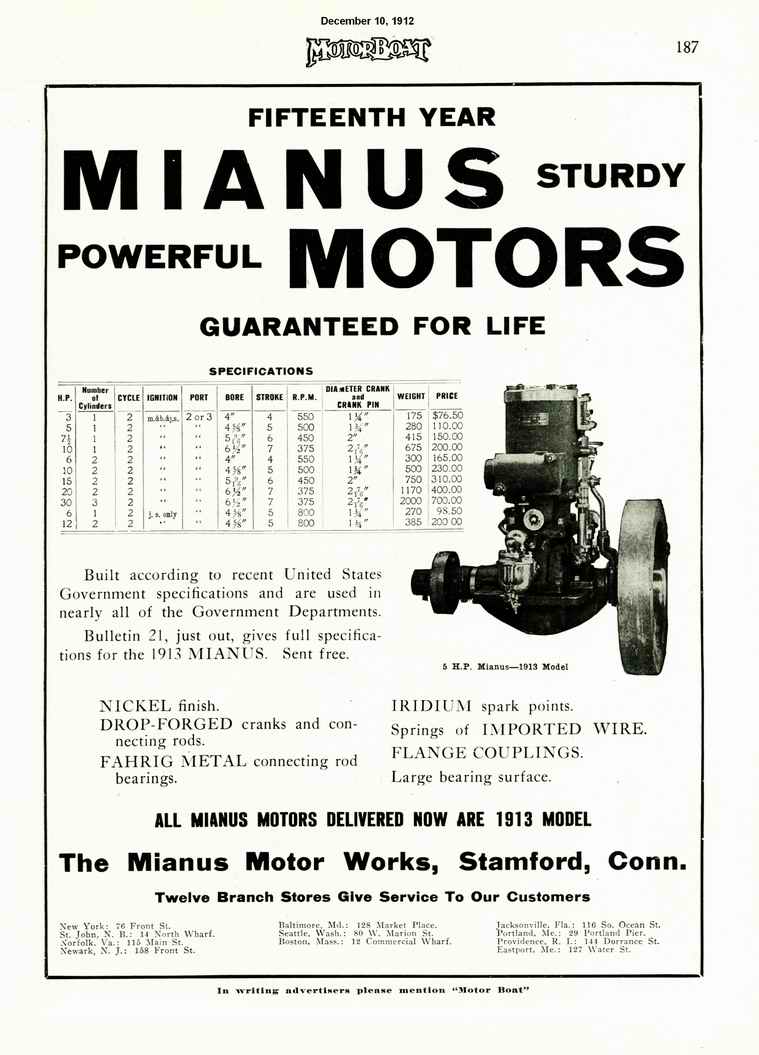 |
   
Richard A. Day Jr.
Senior Member Username: richardday
Post Number: 1000 Registered: 11-2003
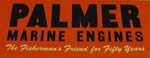
| Posted on Monday, March 26, 2012 - 06:41 pm: |
|
Mianus Motor Works moved from Mianus CT. to Stamford in 1907. When their main office moved to NYC their manufacturing plant remained in Stanford, CT. Today Mianus is a part of Stamford. |