Author |
Message |
   
searcher
Senior Member Username: searcher
Post Number: 344 Registered: 10-2004
| Posted on Monday, September 28, 2009 - 10:33 pm: |
|
I recently bought a headless 2hp inboard marine engine that is stuck. The top of the piston is well above the exhaust port. I plugged the oil cup openings, exhaust opening, etc., filled the cylinder with oil, screwed a grease fitting into the spark plug hole, and commenced pumping grease into the cylinder. The piston moved downward about 1/4" and I then tried to move the piston using a wrench on the prop shaft coupling. The piston is so tight I still cannot move it except with input from the grease gun. The top of the piston remains above the exhaust port. So, before I proceed further, what happens if I pump grease in to the point the piston is bottom dead center and is still too stiff to turn over with a wrench? Should I turn the engine upside down and try to get some lubricant such as WD40 around the bottom edge of the piston (between the piston and the cylinder wall) before I start pumping grease into the cylinder again? Now is my best chance to get it right so I need the input of people much more experienced at this than I am. |
   
jb_castagnos
Senior Member Username: jb_castagnos
Post Number: 477 Registered: 07-2002
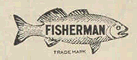
| Posted on Tuesday, September 29, 2009 - 01:17 pm: |
|
You won't get to bottom center, it will quit when the exhaust ports open. If it's moving I think you are in good shape, it wouldn't hurt to try to lube the bottom of the piston. Heat around the oustside of the cylinder helps. Is the cylinder removable, is it a split case or a flange end? |
   
searcher
Senior Member Username: searcher
Post Number: 345 Registered: 10-2004
| Posted on Tuesday, September 29, 2009 - 04:57 pm: |
|
It is a two port, two stroke 2 hp Capital (Augusta, Maine)with a split crankcase as seen in the photo. The second photo is from the Capital catalog. I blocked off the exhaust port but forgot the inlet port would become exposed as soon as the piston passed by the exhaust port. So, the piston probably only has a very short distance to go before the grease fitting in the spark plug hole method no longer works. I was and am apprehensive that the piston will get hung up at that point with no easy way to move it without risking damage. I should have realized that but I have not gotten much into the mechanics of these things yet.
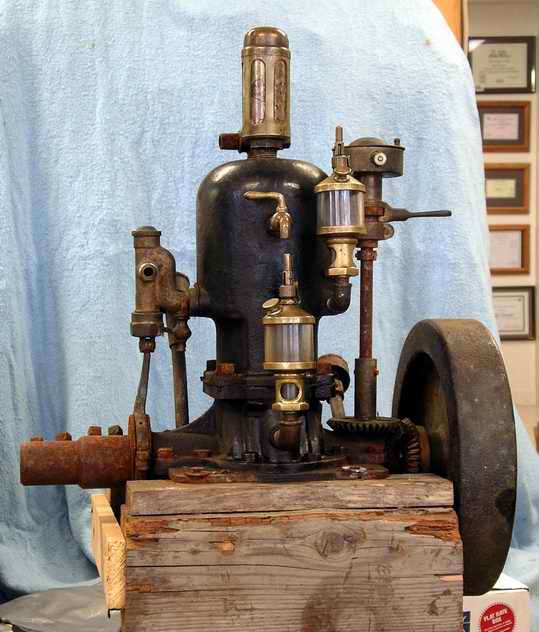 |
   
richardday
Senior Member Username: richardday
Post Number: 812 Registered: 11-2003
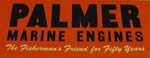
| Posted on Tuesday, September 29, 2009 - 08:04 pm: |
|
Push the piston back in and then push it out again with oil/grease. Repeat a few times and it should come out quite easily. Don't try to pull it out with the con rod until you have really got is loose. I will send you a paper I wrote some years back how to keep from destroying headless engines with stuck pistons. Will try to locate it it is somewhere in my computer. |
   
jb_castagnos
Senior Member Username: jb_castagnos
Post Number: 478 Registered: 07-2002
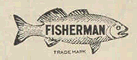
| Posted on Tuesday, September 29, 2009 - 08:22 pm: |
|
Removable cylinder, split crankcase, the easiest to take apart when stuck. Go ahead and pump it down, when it gets low the rod will have a better mechanical advantage, you may be able to start turning it. If not, do as Dick says, take it apart and press it back in, soak it with penetrant, it will wash away the loosened particles. Good looking complete engine, nice find. |
   
searcher
Senior Member Username: searcher
Post Number: 346 Registered: 10-2004
| Posted on Wednesday, September 30, 2009 - 12:08 am: |
|
Between JB's comments and Dick's paper, I could see that I had options. So I split the crankcase, turned the cylinder upside down and every hour or so will spray a little WD-40 into the space between the piston and the cylinder wall. Tomorrow afternoon I will resume with the grease gun. The exposed cylinder wall below the piston was actually very clean. Consequently, it surprises me that the piston moves only when subjected to the great force of the grease gun. Like I say, this is an education since I have not gotten into the mechanics of these things very often. Thank you Dick and JB for the advice. |
   
searcher
Senior Member Username: searcher
Post Number: 358 Registered: 10-2004
| Posted on Friday, October 16, 2009 - 12:44 am: |
|
The advice from JB and Dick gave me the impetus to proceed with extracting the piston. Once I got the piston as far out as I could with the grease, I made up this crude arrangment. The spacer is schedule 80 PVC pipe. I couldn't have imagined getting so lucky but the inside diameter of the PVC pipe was perhaps 1/16" greater than the diameter of the piston, essentially a perfect match. Before actually attempting to extract the piston, I bushed the pipe you see in the connecting rod journal so it was a tight fit. The eye bolt shown sprung right away so I ended up buying a much heavier one. I was some tickled when the piston finally came free and I hadn't broken anything. The baffle on this piston was not what I was expecting. When did this style of piston become available? Two of the rings are broken and I suspect were broken when the engine was last apart. Where is the best place to get a couple of replacement rings?
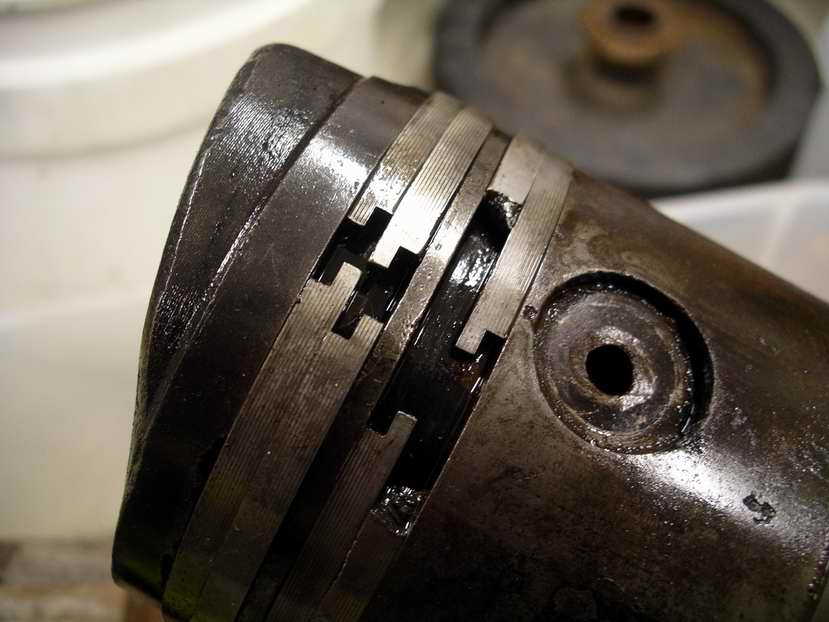 |
   
jb_castagnos
Senior Member Username: jb_castagnos
Post Number: 485 Registered: 07-2002
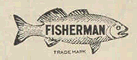
| Posted on Friday, October 16, 2009 - 06:48 am: |
|
Good work. I've seen this style piston before, don't remember what it was on. Usually the lower side of the intake and exhaust ports are even, on this engine the intake is probably lower than the exhaust. Dave Reed at Otto Piston Ring should have rings, they probably won't be stepped and don't need to be, you'll have to file the notch for the pin. The stepped gap looks like it would seal better but compression doesn't travel "line of sight". It will come around the top of the ring as it is being forced to the bottom of the piston, it will build pressure behind the ring helping to force it against the wall, and it will try to escape therough the bottom half of the stepped gap. Early manufacturers made a mistake when they put the locating pins on the bottom side of the rings. if you file a 3/16" gap to clear the pin, that's your ring gap, no matter how tight you fit the ring above the pin. When reworking ring lands I always move the pin to the top of the groove. If you can't find rings you could use a good ring on the bottom of each groove, the top is only acting as a spacer anyway. |
|
|
|
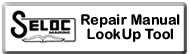

|