Author |
Message |
   
marks
| Posted on Wednesday, August 07, 2002 - 04:31 am: |
|
Hello All, I'm looking for opinions for repairs to cracked water jackets! Bascically I have a couple of CLAE twins(oz motors) which are cracked on the outer water jacket along the bottom. These cracks are maybe 6" long and run over edges. They are due to corrosion. Basically there seem to be a few "schools of thought" on what to do: 1) use the blocks for anchors 2) braze with suitable pre and post heat treatment. 3) chop out sections and glass with suitable fillers(devcon) etc, many variations on this theme. 4) lock and stitch proprietary system. I would like to recover at least one of these engines for use in a boat with freshwater cooling system. I would also like the repairs to be unobtrusive. Option one is sort of out of the question. Brazing when succesful looks a bit messy. Some people say cut and fill but it seems to me that this option is not really suitable for something that is going to be used frequently. I sort of like the approach with the stitch and lock. Has anybody used this system for what is surely weak metal? Any advice is greatly appreciated. BTW the blocks have oil in the water passages but have not really been cleaned. I understand they have been sitting for some ten years. Should i use Peter O's mollases trick? Thanks in advance Mark S. |
   
andrew
| Posted on Wednesday, August 07, 2002 - 09:32 am: |
|
Mark, The real problem is the one sentence you included saying that the cracks "are due to corrosion". I think you will find that if you can't get back to sound metal you will find it impossible to weld, braze, or stitch'n'lock. Epoxy becomes the only alternative in a case of badly corroded iron. Hopefully others will jump in with their opinions. You can also search the board by using the "keyword search" link on the left for words like welding, crack, manifold, etc.... and you will find previous conversations about these topics. Regards, Andrew |
   
Joe
| Posted on Wednesday, August 07, 2002 - 11:23 am: |
|
Mark, I'm on the west coast and most of my project engines were salt water cooled. Most developed cracks while they lay sleeping in some old shed. The cracks are from pressure from within. The rust that forms inside water jackets of cast iron is akin to a tumour. It grows and expands with enormous pressure which bulges, bends, and cracks the jacket. It usually does not crack the bore. To repair the outer water jacket you MUST remove the growth inside the jacket. This stuff is tough and it takes much more than a coat hanger wire. You will probably have to cut windows (openings) at strategic places around the cylinder to enable you to get at the growth. You have to get it out for two reasons; to relieve the pressure and kill the stuff and to recover the area for the coolant to do it's work. You then fit the window pieces back in place, secured with epoxy such as "Weld Bond". Keep in mind that the outer part of the water jacket, for the most part, just keeps the water in. Weld Bond has worked very well for me and does not mess up the looks of your engine. There is some info on this subject some where on this board from Dick Day as well. Be aware that the rust tumour can bend cast iron to the extent that mounting flanges may need to be re-machined, ie cylinder to base. Hey, it's all do-able and the doing is what does it for you. |
   
Richard Day
| Posted on Wednesday, August 07, 2002 - 05:32 pm: |
|
If the cracks are salt water cracks the only alternative is epoxy. It works great as long as you clean off the surface rust so you can get a good bond. I agree with all of Joe's points. Fresh water cracks can be brazed or welded and will last but it takes a real pro to handle the heating and even more important the cooling otherwise you wind up with a badly warped block or worse. Heavy rust build up is essentially always salt water rust and it looks different from fresh water rust. Salt water rust is very hard and it takes real patience to get it out and in one case I dug it out and the cylinder water jacket cracked about a year later due to the stresses that had built up and then releived. Never again will I make that mistake with a good jug. |
   
peter ogborne
| Posted on Friday, August 09, 2002 - 08:21 am: |
|
I can only add to the previous comments all of which are correct. I would not attempt to do a brazing repair as in most cases the parent metal is buggered . The same applies to the Metal lock process. Cutting out and replacing windows is the simple and sure way . I have had engines running at shows at maximum temps. At the last show my water pump intake blocked ,some one had thrown a piece of paper into the water tank. My engine was sure boiling. The epoxy filler held up and is still in place . The one proviso i make is that i have not had any of my repaired engines put to sea. I am sure though relying on a cooling tank on a hot summers day in OZ is a good test, BTW ,I use a product called Epigen 2008. |
   
marks
| Posted on Monday, August 12, 2002 - 12:07 am: |
|
Thank you for your responses. As you all rightly say saltwater causes the problem in the deposits that build up and cause the failure. As well as cylinders I have a head which i would like to fix so i will experiment on it. The cracks are in the outside jacket and also into the combustion chamber, so I don't think epoxy will work. I will try the lock and stitch approach in the combustion chamber. Depending on the results and the amount time it takes I will then make a decision on whch method to use on the outside(expoxy or lock and stitch). I like the idea of the cable in the drill and cutting small holes into the jacket to remove the "tumor". Thanks again, Mark S. |
   
andrew
| Posted on Monday, August 12, 2002 - 08:50 am: |
|
Mark, Lock'n'stitch has some excellect products and good documentation, including a video: http://www.locknstitch.com/ .... but I think it will be tough to do the combustion chamber... keep us posted. Regards, Andrew |
   
Matt Gehman
| Posted on Thursday, April 15, 2004 - 12:31 pm: |
|
Check out www.metalocking.com. They repair water jackets on locomotives to marine. |
|
|
|
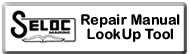

|