Author |
Message |
   
Len Tate
| Posted on Monday, May 13, 2002 - 06:56 am: |
|
I'm trying to get the flywheel off the tapered shaft of the crank on my Blaxland 3.5hp single cylinder engine. My press is only good for 15 tons and that's not enough. I've had it soaking in a penetrating fluid (Penetrene for those who know it) for three weeks but no luck. Any ideas please? |
   
Richard Day
| Posted on Monday, May 13, 2002 - 10:55 am: |
|
Not knowing your set up I can offer the following thoughts. If the crankshaft is out of the engine and in the flywheel what I do is make up a couple of 1/8" thick sheet lead C washers that will fit around the crankshaft and isolate the casting of the flywheel from direct contact with the steel bed of the press. This will insure the any slight rough spot on the flywheel casting doen't take all the load and crack the hub when you press the crankshaft. It is critically important to make up two plates with a hole in the center a few thou larger than the crankshaft. I use 1" steel plate. Cut two slots from the edge of the plate to the center hole . Save the pieces you have cut out of each plate. The plates are then put around the crankshaft with the slots at 180 degrees. slip the two pieces you cut out into to the slots so in effect you now have a 2" thick backing plate all around the crankshaft with the two lead C washers between the backing plate and the fly wheel. When this setup is put in the press with a tapered crankshaft before I try to press the shaft out I take a a short length of bronze shaft and give the tapered end of the crankshaft a few hard knock. Often this will release the taper easier than the steady pressure from the press. If it doesn't then try the press. Don't forget to catch the crankshaft if is going to fall very far. I can tell you from my own experience I ruined a good crankshaft for that very oversight. "Not the brightest in my age group." In any case no heat on the flywheeel. You are creating a ticking time bomb if you do heat it. I have heard of trying dry ice around the steel crankshaft itself to shrink it but no heat on the cast iron flywheel. If the flywheel is captive to the engine I have broken them loose by placing the crankshaft in a vertical position and supporting the edges of the flywheel on a couple of saw horses. This puts the weight of the engine on the crankshaft and if you loosen the crankshaft nut a couple of turns you can then rap the end of the crankshaft with a peice of bronze shaft. I have had good sucess with this approach on solid disk flywheels. I have not tried it on spoked flywheels. For flywheels with badly stuck Gib keys and no need to save the crankshaft I cut off about two inches of the crankshaft behind the flywheel. Place the fly wheel hub on lead washers and steel backing plate. Then push the crankshaft through the hub from the back side. Pushing from the front side will probably crack the hub due to the angle of the Gib key.. From the back you may be lucky enough to drive out the gib key if enough of the keyway is exsposed. Once the key is out continue to drive the shaft out from the rear. Make sure you have cleaned it up as well as possible so it will not further complicate the problem. A little penetrating oil will help in all of these approaches. My experience in withdrawing rusted but not beat up gib keys shows the way to do it is make a bright mark on the key a few thou from the face of the hub of the flywheel. Machine a chunk of steel that will be a good fit in the keyway and in its vertical direction at least as high as the the head of the Gib key. What you are trying to do is get a very straight whack on the gib key so you don't mess up the tang of the key. Take a couple of hose clamps and clamp the driver to the crankshat so it will go straight in when you whack it. Don't try to free hand it. Give it a whack and see if there is any movement of the key. If so then a little penetrating oil will do wonders as it can now get in the cracks around the key. If you can find an old fashioned split rim truck tire tool you will find the small curved end is an excellent tool to pull Gib keys provided someone has not totally messed up the vertical tang on the key. You know what free advice is worth. Good luck and let us know how you make out. |
   
Len Tate
| Posted on Tuesday, May 14, 2002 - 12:42 am: |
|
Richard, Thanks for your help. The crankshaft is out of the engine, and the flywheel is a solid one and is held onto the crank by a taper. The engine is very old -probably early 1930's, and was used in a hire boat in salt water so the taper may have rust in it. Your idea of the lead washers is good and I'll do that.Otherwise I'm doing the same as you. My press is limited to 15 tons and no luck so far. I'll try hitting the end via a bronze rod first and see if that works. |
   
peter ogborne
| Posted on Wednesday, May 15, 2002 - 08:22 am: |
|
Len ,I had to do the same with my Chapman Super Pup . I made a puller using 50 mm RHS ,2 long bolts and a strongback with a 3/4 BSF puller bolt . I also used lead pads between the 50 mm RHS and the fly wheel. I was concious of not putting too much pressure on the pull having buggered a alloy flywheel using the same set up . So medium pressure and a belt with a copper hammer on the crank end . When mine released it came with a hell of a bang but it was off. |
|
|
|
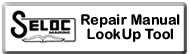

|