Author |
Message |
   
andrew
| Posted on Saturday, October 12, 2002 - 07:56 pm: |
|
Mark Stretch from Australia has submitted two (so far) very detailed articles on the topic of corrosion in the water jackets of saltwater marine engines. He has studied the causes and some of the popular methods of treatment. He has contacted various musuems and conservators and done a very professional job of researching this topic. Thank you Mark for sharing your research with us... See: CORROSION IN SALTWATER MARINE ENGINES |
   
rbprice
| Posted on Saturday, October 12, 2002 - 09:30 pm: |
|
FANTASTIC INFO Mark - Well done. My hearty personal thanks and I suspect, thanks from those of us who ardently follow OME. Bob Price |
   
Richard Day
| Posted on Tuesday, October 15, 2002 - 05:25 pm: |
|
Really excellent article. Would suggest however that Mark make a note that the mechanical removal of the hardened deposits can so change the stresses in the the water jacket that after major removal one may find that in a few months the cylinder outer water jacket wall will crack. I know this from bitter experience. Its one of thos situations where you are dammed if you do and dammed if you don't. I still use the mechanical removal technique but I always hold my breath when I am finished. |
   
marks
| Posted on Wednesday, October 16, 2002 - 01:06 am: |
|
Thanks Andrew, Bob and Richard, Richard I will add the caveat on deposit removal changing or introducing new stresses. At the moment I'm getting the pieces together for an alkaline sulphite treatment setup. Basically my only solution at the moment is to build an insulated box with heating and a suitable pump. The cylinder will have blocking plates attached with plumbing to the pump and a solution reservoir. It would be simpler to immerse the cylinder completely in a suitable container. However the size reqd, about 36" square means this course of action is probably ruled out. Mark S. |
   
Steve OBrien
| Posted on Thursday, October 17, 2002 - 01:25 am: |
|
Thanks MArk for an excellent article. Very timely, as I have just started an attempt to de-clog the waterjacket of my Simplex 3HP. I'm using the electrolytic method with Caustic Soda (Sodium Hydroxide). Trouble is, the battery charger I'm using cuts in and out every 15 seconds, sensing an overcurrent. Any suggestions? |
   
solarrog
| Posted on Thursday, October 17, 2002 - 01:31 am: |
|
Try add some more water to your mix. sounds like your mix is to strong |
   
peter ogborne
| Posted on Thursday, October 17, 2002 - 08:39 am: |
|
Great article Mark ......i have been using the mollasses method for some years now . Great for external corrosion but physical removal for water jackets ,ie chisels etc still the best .I am gradually converting my engines to fresh water cooling with a closed circuit and inhibitor . |
   
marks
| Posted on Thursday, October 17, 2002 - 08:05 pm: |
|
Hi Steve, Re electrolysis. I have used electrolysis with good results, however you should still only consider me an armchair expert. The steps in the electrolysis process depend on the results you are after: 1) Return to Service which is: Unclog and treat the corrosion, with the cylinder to go back into service in a salt water environment. OR 2) Restoration which is: Unclog and treat the corrosion, remove residual chlorides and use the cylinder in a non-seawater cooled environment. The aim is to stop any further detoriation. In either case the setup for electrolysis will be the same. I would urge you not to go the battery charger route. You will need a variable power supply capable of: 1) somewhere between six and 32 volts. 2) sufficient adjustable amperage to give somewhere between 50 and 200 mva per sq inch of metal to be treated. This is the sufrace area of the item including the water jacket area. I notice that you are in Australia. If you are handy with a soldering iron Jaycar etc should be able to sell you a suitable kit or possibly a complete power supply at modest cost. Alternatively if you are comfortable with electronics you could modify a battery charger to suit. BTW I picked up a suitable power supply at auction for $15.00. You are using caustic soda(sodium hydroxide). This should be around 2.5% solution ie about 25grams per litre of water(strictly speaking should be be 975mls). The method will be slighly different depending on whether you are returning to service or restoring. For both restoration and returning to service you should adjust the power supply until there are small bubbles forming on the surface of the cylinder. They should just be forming not bubbling too much. For return to service let this process run until you are happy with the results. You can then increase the power for a mechanical cleaning action(short time only see hydrogen embrittlement). The return to service part is now finished. For restoration you will need some way off measuring the level of chloride within the water jacket. If you wish I can email you details(it will be in the third part of the article). You will need to change the solution when the chloride level plateaus which seems to be about weekly. The process continues until you have reached the desired chloride level < 50ppm. Seawater is @33000ppm. The cylinder will then need further passivation treatment and removal of hard deposits with probably a further electrolysis treatment for the chlorides locked up in the metal under the hard deposits which you removed. Steve in order for electrolysis to be successful the electrode needs to be in a line of sight to the corrosion. If yours is a four stroke simplex with removable head then you may need to rig a series of electrodes which reach down into the jacket. If it is one of the older two stroke castings with combined head and cylinder it will be very difficult. There is a different process called alkaline sulphite which would be more appropriateif this is the case. The process itself is simple however the setup is more complex than electrolysis. One thing to be aware of using electrolysis is hydrogen embrittlement. If you let the process bubble too much it will damage the casting. What effectively happens is that hydrogen gas is produced under the suface of the metal causing microscopic cracks and voids. One other thing is that you should keep the PH of the solution betwwen 10 and 13. If the PH fals outside this range then further accelerated corrosion will occur. PH test strips are readily available from chemical supply companies. If the pH falls outside the range the solution should be changed. Mark S. |
   
marks
| Posted on Thursday, October 17, 2002 - 08:48 pm: |
|
Correction, The power supply should be capable of somewhere between 50 and 200ma per sq foot. I would aim for the 200 if possible. Mark S. |
   
steve obrien
| Posted on Thursday, October 17, 2002 - 09:28 pm: |
|
Thanks so much Mark for your advice. My intention is to return the engine to service.. so it's back to the bucket for me. And there's a jaycar shop nearby. Or is there a recipe for modifying the charger I just bought for someone like me with a soldering iron but v little knowldge of electronics? I see youre at citywest...i did some work on the pyrmont marina when I was at SKM years ago. |
   
marks
| Posted on Saturday, October 19, 2002 - 07:24 pm: |
|
Steve, Because you are commited to the battery charger route here is waht I would do: Try experimenting with the electrode size ie if it is a rod then you can just submerge the tip and keep advancing the rod into the solution until the charger cuts out. Then back the rod out slightly. BTW we are often confused with the Citywest you are talking about. Actually we are a software development co. Hope this helps. If not give me a call on 02 9725 3709 BH or 43 427 559 AH Mark S. |
   
Ernie
| Posted on Sunday, October 20, 2002 - 05:18 pm: |
|
For todays chuckle.........who remembers the cat stuck in the mollasses? My wife enjoys my hobbies, however one of her cats stuck in the muck in my shop just might change here atitude! Hope you all had a good weekend Ernie |
   
poker casino494 Visitor
| Posted on Monday, March 06, 2006 - 01:31 pm: |
|
poker casino poker 171 |
   
poker casino706 Visitor
| Posted on Monday, March 06, 2006 - 04:29 pm: |
|
poker casino poker 245 |
   
poker casino801 Visitor
| Posted on Monday, March 06, 2006 - 04:30 pm: |
|
poker casino poker 724 |
   
Thomas123
Visitor
| Posted on Wednesday, March 18, 2009 - 03:16 am: |
|
Hi, I have a boat motor using raw salt water cooling, I would like to remove some of the salt build up without taking the motor to bits, do’s any one know if there are any commercial products that one can circulate round the water jacket to help slow or reduce the corrosion process whilst the motor is in situ. |
   
richardday
Senior Member Username: richardday
Post Number: 722 Registered: 11-2003
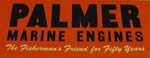
| Posted on Wednesday, March 18, 2009 - 09:27 am: |
|
It seems to me nothing short of high temp cooking will drive the salt out of the pores in cast iron water jackets. I have no confidence in any of the schemes where you use acid to try to clean out the water jacketed part. I beleive they do more damage than good. I suggest putting in a simple keel cooler and if in an area where freezing is likely add anti freeze sufficiant to handle the likely lowest temp. Otherwise circulate fresh water and routinly flush it out to remove as much salt as possible. Basically as long as you don't let the castings dry out let the residual salt remain. But!!! keep it wet!!! |
   
rowella
Member Username: rowella
Post Number: 10 Registered: 06-2008
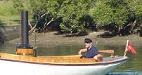
| Posted on Thursday, April 16, 2009 - 07:29 am: |
|
Has anybody found a kit for testing for chorides suitable for elecrolytic bath. The kit I have tried is intended for water at Ph 7 and does not work at Ph 10 or 11 Hope to hear of something available in Australia.martin |
   
searcher
Senior Member Username: searcher
Post Number: 427 Registered: 10-2004
| Posted on Friday, April 16, 2010 - 08:31 pm: |
|
Here is an article from the July 25, 1926 issue of MotorBoat. Has anyone tried this tin chloride method to clean out rust?
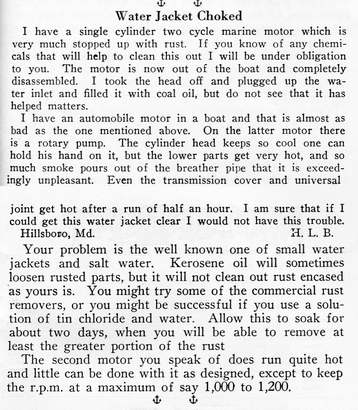 |
   
marks
Senior Member Username: marks
Post Number: 123 Registered: 03-2002
| Posted on Thursday, April 22, 2010 - 06:47 pm: |
|
That's interesting, A quick google search brings up quite a few references. It seems that the tin chloride that is required is Tin(II) Chloride - Stannous Chloride. It is stated as a reducing agent for iron corrosion products as indeed are most of the rust removal/treatment methods. So it seems to me it would definitely be worth investigating. That said it seems it's base state is white crystals that need to be dissolved in hydrochloric acid. It goes without saying that extreme care and appropriate safety gear should be used. The method I use almost exclusively now is electrolysis sometimes with a furnace pre-treatment (to sort out the wheat from the chaff and to loosen hard deposits). It's quick, simple and cost/time effective. Cheers, Mark S. |